Green Morsel – Enquête terrain, données recueillies et Persona – Compost dans les appartements
Enquête terrain, données recueillies et Persona du projet : Green Morsel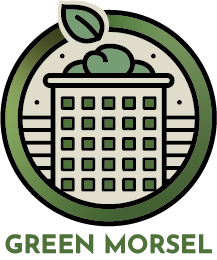
par Mathieu BOSSART, Ethan GOIRAND, Romain LETELLIER, Abner RODRIGUES, Sheryle TOURE
I. Synthèse de l’enquête terrain
A. Rappel des hypothèses
- Hypothèse 1 : Le compostage représente la solution la plus durable pour traiter les déchets alimentaires en France.
- Hypothèse 2 : Les citadins compostent peu ou pas en raison des problèmes olfactifs liés à l’accumulation de déchets alimentaires et du manque de moyens fournis par les municipalités pour acheminer les composts d’appartement.
- Hypothèse 3 : Mauvaise gestion des emplacements des poubelles de tri dans les habitudes des citadins
B. Liste anonymisée des personnes rencontrées
Le tableau ci-dessous présente, de manière anonymisée, les personnes ayant été interviewées :
Les acteurs | Leurs caractéristiques |
Émile Rosbeef, travaillant dans un restaurant Brestois faisant une cinquantaine de couverts par service |
|
Yollande et Ivette, bibliothécaire à la PAM (Brest) |
|
Jean, responsable de la gestion des déchets à Brest métropole |
|
Christophe, Marie, Paul, Antoine et Julie, cinq citoyens habitant à Brest |
|
C. Présentation d’un compte rendu type (Q/A)
Il s’agit du compte rendu d’entretien de la personne chargé de la gestion des déchets pour la Métropole de Brest
Questions | Réponses |
Quels sont les dispositifs mis en place par la Métropole pour collecter et valoriser les déchets alimentaires ? | La métropole travaille principalement avec l’association Vert le jardin (partenaire et prestataire), notamment depuis le changement de réglementation.
Il existe deux manières de valoriser les déchets en ville :
La solution retenue, qui fonctionne le mieux pour valoriser les déchets est la méthanisation, même si elle est coûteuse. |
Observez-vous des difficultés / points bloquants avec ces dispositifs mis en place (notamment avec le compostage collectif) ? | Nous avons noté plusieurs points :
|
Au vu de ce que vous dites, la métropole n’a pas pensé à inciter au compostage individuel ? | Les composteurs individuels sont presque gratuits pour les habitants de maisons.
Cependant, il n’existe pas de solution gratuite pour ceux qui vivent en appartement, et il semble qu’il y ait des opportunités à développer dans ce domaine. Certaines initiatives sont mises en place avec les copropriétés, mais elles nécessitent qu’une personne soit responsable du composteur, car les mêmes problèmes que pour les aires collectives se posent |
D’ailleurs, pour ce qui est du compostage, savez-vous si les odeurs sont un problème ? | L’odeur est bien un problème si le composteur n’est pas équilibré. S’il est bien entretenu (remuer, ajouter des matières sèches…), il ne posera aucun souci. |
D. Synthèse des informations clés récoltées lors des entretiens
a. Émile Rosbeef, travaillant dans un restaurant Brestois
L’entretien avec ce restaurateur expérimenté révèle plusieurs aspects cruciaux de la problématique des déchets alimentaires dans la restauration. Bien qu’il reconnaisse une sensibilisation croissante au tri des déchets alimentaires dans son secteur, il met en lumière un paradoxe important : malgré une conscience environnementale personnelle, la gestion des déchets et des invendus ne constitue pas une priorité économique dans son établissement. Son témoignage souligne l’importance des incitations économiques, suggérant que la majorité des restaurateurs ne s’engageront dans le compostage qu’en présence d’avantages financiers, comme une réduction des taxes. Il pointe également une problématique concernant la saturation des associations de redistribution des invendus, ainsi qu’un manque général d’information sur les pratiques de compostage dans le secteur de la restauration.
Verbatims : “Il reste encore beaucoup de chemin à parcourir en ce qui concerne le compostage des déchets pour les pros”
b. Yollande et Ivette, bibliothécaire à la PAM (Brest)
Yollande et Ivette, bibliothécaires à la PAM Ces deux bénévoles de la librairie solidaire offrent un éclairage intéressant sur les freins au compostage domestique en milieu urbain. Bien qu’elles pratiquent consciencieusement le tri des déchets alimentaires avec des poubelles dédiées, elles expriment une réticence envers le compostage à domicile. Leurs réserves s’articulent autour de deux obstacles majeurs : le manque d’espace dans leur logement et les craintes liées aux odeurs. Leur préférence pour l’utilisation des poubelles de quartier, couplée à leur désintérêt pour des formations ou du matériel supplémentaire, suggère que les solutions collectives peuvent être plus adaptées pour certains profils d’habitants.
c. Christophe, Marie, Paul, Antoine et Julie, cinq citoyens habitant à Brest
Ce groupe de citoyens engagés, âgés de 25 à 40 ans, apporte un éclairage sur les conditions de réussite du compostage urbain. Leur expérience démontre l’importance de la gratuité des équipements dans l’adoption des pratiques de compostage, tout en indiquant qu’un investissement modéré (50-100€) reste acceptable pour du matériel de qualité. Ils contestent l’idée reçue sur les nuisances olfactives, affirmant qu’un bon entretien suffit à les éviter. Leur témoignage met cependant en évidence une difficulté pratique majeure : le manque de clarté concernant la localisation des points de collecte des déchets alimentaires. Ils soulèvent également une préoccupation importante concernant les systèmes de rémunération du tri, citant l’exemple du Danemark où ces incitations ont eu des effets sociaux pervers, encourageant l’abandon des déchets pour leur collecte par les personnes sans abri.
d. Jean, responsable de la gestion des déchets à Brest métropole
Fort de ses 15 années d’expérience à la Métropole de Brest, Jean apporte un éclairage technique et pratique sur la gestion des déchets urbains. Son analyse révèle que la méthanisation, bien que plus coûteuse, s’avère plus efficace que le compostage en milieu urbain. Il identifie plusieurs défis majeurs concernant les aires de compostage collectives, notamment la prolifération des rats et la mauvaise qualité du compost due aux pratiques inappropriées des habitants. Son témoignage met également en lumière une inégalité structurelle : alors que les propriétaires de maisons bénéficient de composteurs quasi-gratuits, aucune solution équivalente n’existe pour les habitants d’appartements. Il apporte aussi une nuance concernant les odeurs, soulignant qu’elles ne deviennent problématiques qu’en cas de mauvais entretien du compost.
Verbatims : “Les rats sont un frein à l’utilisation des composteurs collectifs”
E. Conclusion partielle
Concernant l’hypothèse 1, les entretiens, notamment avec Jean de la métropole de Brest, apportent une vision plus nuancée du traitement des déchets alimentaires en milieu urbain. Si la méthanisation s’avère plus efficace en termes de traitement des volumes importants, malgré son coût plus élevé, l’enquête suggère qu’une approche hybride pourrait être plus pertinente. En effet, le compostage et la méthanisation apparaissent comme deux solutions complémentaires plutôt que concurrentes
L’hypothèse 2 est partiellement validée mais nécessite des nuances importantes. Si le manque de moyens municipaux est confirmé, particulièrement pour les habitants d’appartements qui n’ont pas accès aux mêmes solutions gratuites que les maisons individuelles, la question des odeurs apparaît davantage comme un problème lié à une mauvaise utilisation collective des composteurs que comme un obstacle technique réel. Les témoignages convergent : un compost bien entretenu ne génère pas de nuisances olfactives.
L’hypothèse 3 est clairement confirmée par l’ensemble des témoignages, avec une difficulté particulière concernant la localisation des points de collecte des déchets alimentaires.
II. Persona
Il s’agit de traduire les données recueillies au cours de la préparation de l’état de l’art mais surtout durant le travail de terrain sous la forme de profils types d’utilisateurs (aussi appelés persona).
Pour que Suzanne adopte le compostage, il est essentiel de la rassurer sur la simplicité du processus et sur l’absence de nuisances comme les odeurs ou les rats. Un dispositif léger et ergonomique, associé à un programme de sensibilisation simple et accessible, pourrait la convaincre de s’engager durablement dans la gestion de ses déchets organiques.
Pour qu’Ethaner adopte le compostage, il est essentiel de lui fournir une solution simple, rapide à mettre en place, sécurisée pour les enfants, et adaptée à la taille de son logement. Une aide au tri, un accompagnement sur l’utilisation du compost produit, ainsi que la possibilité d’impliquer ses enfants pourraient lever ses dernières réticences et encourager sa famille à s’engager davantage dans la gestion des déchets.
WaterWatch –Enquête terrain et persona – Eau et agriculture
Arrieta Emanuell, Carrijo Alex, Duval Evan,
Jean-Philippe, Vidart Joaquin
Hypothèses:
- Hypothèse 1: Les producteurs agricoles ont souvent une utilisation inefficace de l’eau, principalement en raison des problèmes de fuites dans leurs canalisations, ce qui entraîne un gaspillage de cette ressource.
- Hypothèse 2: La mise en place d’un solution automatique, qui contrôle et surveille les fuites dans les canalisations, pourrait considérablement optimiser l’utilisation de l’eau dans le secteur agricole, améliorant ainsi l’efficacité de sa gestion.
- Hypothèse 3: À l’heure actuelle, il n’existe pas de technologies spécifiquement adaptées au secteur agricole pour résoudre efficacement le problème des fuites dans les canalisations.
- Hypothèse 4: Le coût de mise en œuvre des systèmes automatique dans les canalisations agricoles est un facteur qui limite leur adoption, empêchant ainsi les petits et moyens producteurs d’optimiser l’utilisation de l’eau.
Contacts:
Présentation du développement de la recherche sur le terrain:
Lors de la réalisation des enquêtes, nous avons divisé les territoires en deux grandes zones. D’une part, l’Uruguay, un pays où prédomine la production bovine en système extensif, avec un climat relativement homogène sur l’ensemble de son territoire. D’autre part, la France, où nous nous sommes concentrés sur la région de la Bretagne et le nord du pays, caractérisés par un climat humide et des précipitations relativement constantes tout au long de l’année.
En ce qui concerne les producteurs uruguayens, trois d’entre eux, ayant des exploitations de différentes tailles, ont été contactés. Le premier, Felipe, est propriétaire d’une exploitation de 170 hectares dans le sud-ouest de l’Uruguay, principalement dédiée à la production laitière avec 100 vaches laitières. Depuis 10 ans, il dispose d’un système d’approvisionnement en eau pour les animaux, utilisant environ 4 kilomètres de canalisations. Ce système a permis d’augmenter la production et d’améliorer la gestion des pâturages.
Le deuxième producteur, Pablo, possède une exploitation de 875 hectares dans le centre-nord du pays, dédiée à l’élevage de bétail en système d’engraissement. Il y a 4 ans, il a mis en place un système de pâturage rotatif, ce qui a nécessité un investissement important dans les systèmes d’eau. Actuellement, il dispose d’un réservoir de 100 000 litres et de trois réservoirs de 80 000 litres, ainsi que d’environ 30 abreuvoirs répartis sur toute l’exploitation et 4 kilomètres de canalisations. Cela lui a permis d’améliorer la production de viande et la qualité des pâturages.
Enfin, Agustín possède une exploitation de 2400 hectares dans le centre de l’Uruguay, avec des activités diversifiées, incluant le cycle complet d’engraissement, de la recrue au bétail prêt à l’abattage, ainsi que des semences de prairie et la production de céréales. Son système d’approvisionnement en eau, conçu pour abreuver les animaux, est divisé en trois parties, chacune avec son propre système d’eau. Chaque secteur dispose d’un réservoir de 100 000 litres et de plus de 5 kilomètres de canalisations. À l’avenir, Agustín n’exclut pas d’utiliser ces installations pour développer d’autres secteurs productifs.
Certains des commentaires clés de ces interviews avec les producteurs uruguayens peuvent être trouvés ci-dessous :
- Felipe:
« Les pannes apparaissent quand il commence à faire chaud (…) quand ils arrêtent de boire de l’eau, le tuyau chauffe et éclate. »
« Ça, en été, ça nous rend un peu fou, tous les jours ou tous les deux jours, on a ce problème. »
« Quand on voit que la pompe ne s’arrête pas pendant longtemps, on commence à suspecter qu’il y a un problème. » - Pablo:
« Nous avons mis en place des systèmes indépendants pour qu’une panne ne désorganise pas tout le système. »
« On pense toujours à comment organiser le contrôle du système, aujourd’hui nous avons 46 abreuvoirs (…) les problèmes viennent surtout des abreuvoirs. »
« Les problèmes ne sont pas fréquents, peut-être une ou deux fois par mois (…) mais quand il y a des pannes, nous perdons toute la réserve. »
« Il faut aller tous les jours, (…) à certaines périodes deux fois par jour, (…) parfois juste pour vérifier qu’il n’y a pas d’eau là où il ne devrait pas y en avoir. »
« Bien qu’il n’y ait pas de moyen d’automatiser la fermeture d’une vanne ou de localiser une fuite, je pense que c’est intéressant, parce que si un tuyau reste cassé pendant 4 ou 5 heures, on perd tout le réservoir (…) et je pense que c’est pertinent, car certains jours, on a du temps, mais d’autres non. » - Agustín:
« Les vannes se salissent et commencent à fuir. »
« Maintenant que tout s’est stabilisé, un problème apparaît au moins une fois par semaine (…) surtout dans les parcelles qui sont éloignées. »
« Au début, ça nous a rendus fous, on avait des fuites tous les jours. »
« La solution, c’est l’observation par celui qui est sur place (…) sinon, la lumière qui est connectée à la pompe reste allumée trop longtemps, c’est comme ça qu’on le sait. »
« Étant donné que les parcelles sont séparées, c’est difficile de savoir s’il y a un problème ou non (…) quand on s’en rend compte, on a déjà gaspillé beaucoup d’eau. »
Maintenant, en ce qui concerne les producteurs français, trois d’entre eux ont également été contactés, tous avec une exploitation agricole différente et de tailles variées. Pour le premier d’entre eux, nous avons la ferme de l’Oncle JP, un agriculteur céréaliers situé en Charentes-Maritimes. Il utilise un système de tuyauteries de 7 km, datant de 1963, pour irriguer ses champs de céréales. Depuis 2000, il remplace progressivement ces tuyaux en fonte par des tuyaux en PVC en raison des fuites fréquentes, dans un projet coûteux estimé entre 500 000 et 600 000 euros. De plus, il fait face à des défis liés aux restrictions croissantes sur les produits herbicides et aux conditions climatiques extrêmes telles que les tempêtes et les sécheresses. Cela, couplé à l’augmentation des coûts énergétiques, souligne la nécessité d’optimiser l’irrigation pour maintenir la rentabilité de son exploitation.
Le deuxième producteur, Le Jardin de KerJean, se trouve à Brest, en Bretagne, et gère une exploitation de 19 hectares, dont il consacre de 2 à 3 hectares à la culture de légumes selon des pratiques d’agriculture raisonnée. Son approche repose sur la vente directe et un système de gestion de l’eau en circuit fermé, qui inclut la récupération des eaux pluviales et un puits pour l’irrigation goutte à goutte. Ayant abandonné l’agriculture intensive, il cherche à limiter le gaspillage d’eau et à promouvoir un modèle de production plus durable et diversifié.
Enfin, la Ferme de Julien, également en Bretagne, gère 102 hectares dédiés à l’élevage de 100 vaches. L’irrigation de ses champs repose sur des eaux grises provenant de stations de méthanisation, bien que celles-ci soient peu riches en nutriments. Cela signifie qu’il ne dispose pas d’un système d’irrigation utilisant des canalisations. Julien est confronté à des coûts énergétiques croissants liés à l’équipement, en particulier dans la salle de traite et pour la ventilation. Bien qu’il bénéficie de conditions favorables pour la gestion des eaux de pluie dans la région, il doit gérer les risques de saturation des sols lors de fortes précipitations. Pour optimiser la gestion de son élevage et de ses ressources en eau, Julien utilise diverses applications mobiles de suivi.
Conclusions selon les hypothèses :
- Utilisation inefficace de l’eau (Hypothèse 1) : Les entretiens avec les producteurs agricoles en Uruguay et en France corroborent que l’utilisation de l’eau est souvent inefficace, principalement en raison de problèmes de fuites et de pannes dans les systèmes d’approvisionnement. Felipe a souligné comment les tuyaux peuvent éclater avec la chaleur, ce qui entraîne un gaspillage significatif d’eau, et comment l’inquiétude constante concernant les fuites affecte le fonctionnement quotidien de son exploitation. De même, Agustín a également mentionné des problèmes fréquents liés à l’état des vannes. Enfin, en ce qui concerne la ferme de l’Oncle JP, il a relaté que depuis 2000, il a dû changer tout son système de tuyauteries pour un plus résistant en raison des fuites fréquentes, ce qui souligne la réalité de nombreux producteurs qui luttent avec l’inefficacité dans la gestion de leurs ressources en eau.
- Optimisation grâce à solution automatique (Hypothèse 2) : La mise en œuvre de systèmes automatisé pour surveiller et contrôler les fuites dans les tuyauteries pourrait offrir une solution viable pour optimiser l’utilisation de l’eau. Pablo et Agustín ont exprimé le besoin d’un meilleur contrôle et suivi, car la possibilité d’avoir un système alertant sur les pannes ou les fuites en temps réel pourrait non seulement prévenir le gaspillage d’eau, mais aussi réduire la charge de travail des producteurs, qui doivent actuellement effectuer des inspections manuelles fréquentes.
- Manque de technologies adaptées (Hypothèse 3) : Les témoignages des producteurs indiquent qu’il n’existe actuellement pas de technologies spécifiquement adaptées pour aborder efficacement le problème des fuites dans le secteur agricole. Malgré l’importance d’une observation constante et d’un contrôle manuel, comme l’a souligné Agustín, cela n’est pas suffisant pour éviter le gaspillage.
- Coût de mise en œuvre (Hypothèse 4) : Le coût de mise en œuvre de systèmes IoT demeure un obstacle significatif pour de nombreux petits et moyens producteurs. Bien que les producteurs reconnaissent la nécessité d’améliorer leurs systèmes, le manque de ressources pour des investissements significatifs peut limiter l’adoption de technologies avancées.
Partie 2 : Personna :
Personna n°1: Sophie
Nous avons identifié les caractéristiques de Sophie Lequeffic en nous basant sur des recherches et une étude terrain ciblée sur le secteur agricole, en particulier les coopératives maraîchères en France. Nous avons choisi de lui attribuer un âge de 38 ans et une expérience de 15 ans, car ces éléments reflètent un profil réaliste d’une agricultrice expérimentée, souvent observée dans ce domaine. Cela justifie son expertise en gestion des cultures ainsi que son engagement envers l’agriculture durable, une tendance marquée chez les professionnels confrontés aux enjeux environnementaux actuels.
Nous avons également identifié des objectifs concrets, tels que l’optimisation de l’irrigation et la recherche d’un bon rendement. Ces objectifs sont récurrents parmi les agriculteurs interrogés, qui doivent sans cesse adapter leurs pratiques face aux conditions climatiques imprévisibles. Les défis comme le dérèglement climatique, les nuisibles, et les réglementations croissantes sur les produits de traitement reflètent les contraintes souvent citées lors de nos échanges avec les acteurs du secteur, confirmant la pertinence de les inclure dans le profil de Sophie.
En ce qui concerne les tendances positives, nous avons constaté une forte demande pour les produits biologiques et un soutien sous forme de subventions de l’État. Ces aspects apparaissent comme des opportunités importantes pour les agriculteurs, leur offrant une stabilité relative sur le marché. Par ailleurs, nous avons souligné l’intérêt pour l’automatisation et les nouvelles technologies, en réponse aux retours fréquents sur le manque de main-d’œuvre qualifiée. Cela traduit un besoin d’efficacité accru et un pragmatisme chez les maraîchers.
Enfin, les traits de personnalité attribués à Sophie, tels que son engagement, sa motivation et sa collaboration, découlent de nos observations sur le fonctionnement des coopératives agricoles. Le travail en équipe et l’entraide sont essentiels dans ce contexte, ce qui explique pourquoi nous avons insisté sur ces qualités, souvent valorisées par les professionnels du secteur. Ces éléments rendent le profil de Sophie cohérent avec les réalités du terrain et les attentes du secteur agricole.
Personna n°2: Carlos
Nous avons identifié les caractéristiques de Carlos García en nous basant sur des recherches et des études portant sur le secteur de l’élevage, en particulier sur les besoins de production et de durabilité auxquels sont confrontés des professionnels expérimentés. Nous lui avons attribué l’âge de 54 ans et 30 ans d’expérience, ce qui reflète le profil d’un éleveur possédant une expertise approfondie en gestion agricole. Son long parcours démontre sa capacité à relever les défis de production tout en cherchant des innovations répondant aux exigences environnementales et économiques.
Nous avons également identifié des objectifs concrets, tels que l’amélioration du contrôle de l’irrigation pour mieux gérer les vastes surfaces cultivées, optimiser l’utilisation des ressources en eau et maintenir un rendement optimal. Ces priorités, régulièrement mentionnées par les agriculteurs interrogés, soulignent leur besoin d’adapter constamment leurs pratiques face à des conditions climatiques imprévisibles et à une forte pression économique. En particulier, Carlos, confronté aux coûts élevés de production, cherche des solutions pour compenser ces dépenses tout en respectant les normes environnementales croissantes. Les défis liés au dérèglement climatique, aux nuisibles et aux réglementations renforcent l’importance d’inclure ces enjeux dans son profil, illustrant une réalité commune à de nombreux acteurs du secteur agricole.
Parmi les tendances positives, nous avons noté une adoption croissante des pratiques alignées sur les critères ESG, devenues essentielles dans l’agriculture moderne. Ces approches, axées sur la durabilité environnementale, la responsabilité sociale et une gestion rigoureuse, offrent aux agriculteurs des opportunités pour se différencier sur le marché tout en répondant aux attentes des consommateurs et des régulateurs. De plus, le potentiel des grandes surfaces agricoles et la fertilité des sols constituent des atouts majeurs, renforçant les perspectives de rendement élevé et d’exploitation durable. Ces éléments témoignent d’un secteur tourné vers l’innovation et la résilience.
Nous concluons que les traits de personnalité les plus adaptés à Carlos sont la résilience, la détermination et le pragmatisme, des qualités indispensables dans le secteur de l’élevage. Sa capacité à s’adapter rapidement et son engagement constant envers des solutions durables et innovantes en font un atout précieux pour relever les défis du secteur. Ces caractéristiques alignent parfaitement son profil avec les exigences du terrain et les attentes des acteurs agricoles face aux enjeux actuels.
Références bibliographiques
[1] « A. J Whittle, et al. Sensor Networks for Monitoring and Control of Water Distribution Systems. Dans Proceedings of the International Conference on Structural Health Monitoring of Intelligent Infrastructure, 6, Hong Kong. 2013. Disponible sur:
https://dspace.mit.edu/handle/1721.1/92764.
[2] « Aides à La Gestion de La Ressource En Eau En Exploitation Agricole. Disponible sur:
[3] « A. Merino. ¿Cuánta agua se destina a la agricultura en el mundo?, El Orden Mundial EOM, 2023. Disponible sur:
https://elordenmundial.com/mapas-y-graficos/cuanta-agua-se-destina-a-agricultura-mundo/?form=MG0AV3
[3] « Bertoleti, P. Projetos Com ESP 32 e LoRa. 2019. Disponible sur:
https://www.google.fr/books/edition/Projetos_com_ESP32_e_LoRa/fnCiDwAAQBAJ?hl=pt-BR&gbpv=1.
[4] « Buena Huella. 2023. Disponible sur:
https://buenahuella.com.ar/productos.php#monitoreo.
[5] « Chartzoulakis, K., and M. Bertaki. Gestion Durable de l’eau En Agriculture Face Au Changement Climatique. Agriculture and Agricultural Science Procedia. 2015. Disponible sur: https://www.sciencedirect.com/science/article/pii/S2210784315000741.
[6] « De Varennes, E. M., and P. Mendonça. Automaticité Des Stations de Pompage Des Réseaux d’irrigation, d’assainissement Agricole et de Distribution Rurale d’eau Potable. 1970.
[7] « Enjeux Environnementaux : L’eau, Les Sols. 28 May 2021. Disponible sur:
https://agriculture.gouv.fr/enjeux-environnementaux-leau-les-sols.
[8] « IrriControl. 2024. Disponible sur:
https://irricontrol.com.br/servicos/.
[9] « Kivoy. 2024. Disponible sur:
https://kivoy.com.uy/catalogo/.
[10] « Le Règlement Général Sur La Protection Des Données (RGPD). 11 Apr. 2023. Disponible sur:
https://www.economie.gouv.fr/entreprises/reglement-general-protection-donnees-rgpd.
[11] « L’eau et l’agriculture. Disponible sur:
https://www.artois-picardie.eaufrance.fr/qui-contacter-a-propos-de/l-eau-et-l-agriculture/.
[12] « Lorentz. Produits Connectés. 2024. Disponible sur:
https://www.lorentz.de/es/productos-y-tecnologia/productos/connected/.
[13] « Pourquoi l’eau Est-Elle Au Cœur Des Enjeux ? Quels Scénarios Possibles Dans Un Contexte de Dérèglement Climatique ?. Disponible sur:
[14] « Résultat Économique Des Exploitations Agricoles et Revenu Des Agriculteurs, Une Très Grande Hétérogénéité. 27 Feb. 2024. Disponible sur:
Green Morsel – État de l’art – Compost dans les appartements
État de l’art du projet : Green Morsel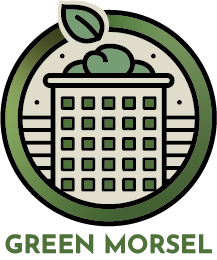
par Mathieu BOSSART, Ethan GOIRAND, Romain LETELLIER, Abner RODRIGUES, Sheryle TOURE
I. Présentation du problème
A. Contexte général
La production de déchets alimentaires a atteint des proportions alarmantes, avec près de 8,8 millions de tonnes de déchets produits chaque année en France. Ce qui représente 129 kg par personne et par an. Parmi ces déchets, 66 kg sont non comestibles, tandis que 63 kg représentent des aliments encore consommables[1]. Cette gestion inefficace de nos ressources alimentaires contribue directement à la pollution des sols, de l’eau et de l’air. Face à cette situation, il devient essentiel de repenser nos habitudes de consommation et de mieux gérer nos déchets afin de réduire notre empreinte écologique.
Il y a ainsi deux types de pollution associés à la problématique de l’excès des déchets alimentaires: d’une part, la surproduction alimentaire, qui est en partie liée au gaspillage ; et d’autre part, la production inévitable de déchets alimentaires, même en l’absence de gaspillage.
Le compostage s’est imposé comme une solution écologique pour valoriser les déchets organiques. En plus de limiter la pollution liée au transport, aux émissions de gaz dans les décharges et aux fumées d’incinération, il encourage la biodiversité locale sans nécessiter de produits chimiques. Cependant, cette pratique, courante en zones rurales, rencontre des difficultés en milieu urbain. Les contraintes d’espace, les nuisances olfactives et les coûts associés à son entretien freinent son développement dans les villes. La question reste donc de savoir comment rendre le compostage plus accessible et pratique pour les citadins.
B. Acteurs concernés et interactions observées
Le tableau ci-dessous présente les principales parties prenantes impliquées dans la problématique du compostage en milieu urbain, ainsi que leurs caractéristiques :
Les acteurs | Leurs caractéristiques |
Les citoyens et les ménages vivant en ville |
|
Les collectivités locales (municipalité et métropole) |
|
Les organisations non-gouvernementales (ONG) |
|
Les entreprises de gestion des déchets |
|
Les startups innovantes en matière de recyclage et de compostage des déchets |
|
Les producteurs de déchets en masse (agriculteurs, restaurateurs, etc.) |
|
Les citoyens, avec des niveaux de motivation variables, dépendent des infrastructures mises en place par les collectivités locales, qui jouent un rôle crucial dans la gestion des déchets et la sensibilisation. Les ONG collaborent souvent avec les municipalités pour promouvoir le compostage, tandis que les entreprises de gestion des déchets et les startups innovantes apportent des solutions technologiques adaptées aux contraintes urbaines. Enfin, les producteurs de déchets en masse, comme les restaurateurs, sont motivés par la réduction de leur empreinte écologique et peuvent influencer la demande de services de compostage.
II. Écosystème visé
Pour définir l’écosystème du projet de compostage en milieu urbain, nous avons effectué une analyse PESTEL (Politiques, économiques, sociaux, technologiques, environnementaux et légaux) détaillée. Le tableau ci-dessous présente les différents volets de cette analyse et les problématiques associées à chacun d’eux.
A. Politique
Pression Écologique et les Objectifs de Réduction des Déchets
Sous la pression écologique croissante, les gouvernements se sont engagés à réduire drastiquement les volumes de déchets incinérés, visant notamment à limiter le volume global des déchets à 2 tonnes par habitant d’ici 2050. Parallèlement, les politiques locales et nationales sont influencées par les engagements internationaux, tels que les Objectifs de Développement Durable (ODD) des Nations Unies, qui encouragent une gestion durable des ressources. En particulier, l’ODD 12 appelle à une réduction significative du gaspillage alimentaire tout au long des chaînes de production et de consommation.
La Réglementation en France au niveau national
En France, plusieurs lois ont été promulguées ces dernières années afin de réduire et de mieux gérer nos déchets. La loi Garot, adoptée en 2016, a marqué une étape importante dans la lutte contre le gaspillage alimentaire. Elle oblige les grandes surfaces à faire don de leurs invendus alimentaires à des associations caritatives et interdit la destruction volontaire de denrées encore consommables [2]. Plus récemment, la loi de février 2020 contre le gaspillage et pour l’économie circulaire (AGEC) [3] a étendu ces efforts à l’ensemble des déchets ménagers. Elle impose notamment à tous les foyers de disposer d’une solution de tri à la source pour les biodéchets dès le 1er janvier 2024. Cela inclut la mise en place de « bio-seaux » dédiés qui seront collectés par des camions spécifiques pour acheminer ces déchets vers des installations de compostage ou de méthanisation.
Cependant, des obstacles persistent, notamment dans les zones urbaines où l’installation de composteurs partagés ou individuels se heurte souvent à des restrictions d’espace, une mauvaise utilisation des installations par les citoyens ou encore par une mauvaise application de la loi initiale. En effet, selon plusieurs associations dont Zero Waste France et France Nature Environnement, la loi AGEC de 2020 a échoué à atteindre ses objectifs de réduction des déchets [4]. Les associations critiquent un lobbying industriel intense, un manque de contrôles et de sanctions, ainsi que des moyens insuffisants pour faire appliquer la loi. Par exemple, un décret de 2023 a permis 29 exemptions à l’interdiction d’emballage plastique pour certains légumes, ce qui remet en cause l’efficacité de la loi [5].
Les Initiatives locales : le cas de la métropole de Brest
La métropole de Brest a mis en place plusieurs initiatives pour améliorer la gestion des déchets sur son territoire dans une démarche globale visant à répondre aux nouvelles réglementations nationales. Ces informations nous ont été fournies par un employé de la métropole travaillant dans la gestion des déchets chez les professionnels.
La métropole a déployé trois approches complémentaires pour encourager le compostage et la valorisation des biodéchets :
- Composteurs individuels : Des composteurs sont proposés à un prix très avantageux, presque gratuitement, aux habitants résidant en maison. Cette initiative vise à promouvoir le compostage domestique et à réduire la quantité de déchets organiques dans les ordures ménagères. [6]
- Abri-bacs : De nouvelles poubelles, appelées abri-bacs, ont été installées dans la ville. Ces conteneurs spéciaux sont collectés deux fois par semaine et leur contenu est acheminé vers des centres de méthanisation pour être valorisé. [7]
- Aires de compostage collectif : Plus de 200 aires de compostage collectif ont été mises en place à travers la métropole, offrant une solution de proximité pour les habitants, particulièrement ceux vivant en appartement. [8]
D. Technologique
Le marché du compost est influencé par diverses technologies qui visent à optimiser le processus de décomposition et à améliorer la qualité des produits finaux. Les différentes méthodes de compostage, telles que le lombricompostage, le compostage aérobie ou encore les composteurs à tambour, ne représentent pas une menace directe pour le marché du compost, mais elles influencent les préférences des consommateurs. Le lombricompostage, par exemple, qui utilise des vers pour accélérer la décomposition des matières organiques, est particulièrement populaire en extérieur car il permet de produire du terreau plus rapidement tout en étant respectueux de l’environnement.
De plus, les innovations technologiques dans le domaine du compostage sont nombreuses. Par exemple, des composteurs intelligents équipés de capteurs IoT permettent de surveiller en temps réel la température, l’humidité et l’aération du compost. Ces données sont cruciales pour garantir un processus de décomposition optimal et réduire les risques de fermentation ou de mauvaise gestion des déchets organiques. Ce type de technologie pourrait se démocratiser dans les zones urbaines, facilitant le compostage même dans les espaces réduits. Nous avons déjà quelques exemples sur le marché.
Une autre innovation potentielle pour le marché est le développement de plateformes d’échange de compost. Ces plateformes permettraient aux particuliers et aux entreprises de vendre ou d’échanger leurs surplus de compost ou de terreau, créant ainsi une économie circulaire à l’échelle locale. De telles initiatives offriraient non seulement un débouché économique pour les producteurs de compost, mais inciteraient également davantage de citadins à se lancer dans cette pratique en leur donnant une finalité tangible à la gestion de leurs déchets organiques.
Enfin, les innovations en matière de biotechnologie jouent également un rôle clé dans le traitement des déchets organiques. Des enzymes et des micro-organismes spécifiques sont développés pour accélérer la décomposition des déchets et améliorer la qualité des composts produits. Ces avancées permettent de réduire le temps de compostage tout en garantissant un terreau plus riche et plus fertile, augmentant ainsi l’attrait pour ces technologies auprès des utilisateurs, qu’ils soient particuliers ou entreprises.
Ces technologies offrent donc des opportunités de marché significatives en répondant à la demande croissante pour des solutions durables. Cependant, elles comportent aussi des défis, tels que les coûts initiaux élevés des composteurs technologiques ou les régulations strictes entourant la vente de certains sous-produits comme les eaux souillées.
C. Sociologique
Les pratiques de compostage des Français
En France, les ménages représentent une source significative de déchets alimentaires, étant responsables de près de 46 % de la production totale, selon une étude du ministère de l’Agriculture publiée en 2022. Cette étude révèle que sur les 4,1 millions de tonnes de déchets alimentaires générés par les ménages, une grande partie (59 %) est constituée de déchets non comestibles, tels que les épluchures, les os et les coquilles d’œufs. Environ 1,7 million de tonnes de déchets, considérés comme gaspillage alimentaire, incluent 1,3 million de tonnes de restes de repas et 0,3 million de tonnes de produits encore emballés. Malheureusement, seulement 13,5 % de ces déchets sont compostés, que ce soit à domicile ou par le biais de systèmes de compostage partagé. [11]
Une forte disparité entre le milieu rural et le milieu urbain
Bien que plus de 4 Français sur 10 déclarent pratiquer le compostage, cette pratique est plus répandue chez les habitants des zones rurales que chez ceux des zones urbaines [11]. En effet, près de 90 % des personnes qui compostent le font dans leur jardin, ce qui témoigne d’une forte disparité entre les modes de vie citadins et ruraux. Selon une enquête de 2020 réalisée par OpinionWay pour l’ADEME, seulement 34 % des Français affirment traiter leurs restes alimentaires par le compostage. [12]
Les obstacles au compostage en milieu urbain
Plusieurs raisons expliquent la faible adoption du compostage chez les citadins. Une série de documents issus d’une étude identifie ces obstacles. NB : Réalisée en 2020, cette étude [11] pourrait voir ses chiffres évoluer avec la législation actuelle.Figure 2 : Étude sur les raisons du non-compostage chez les citoyens
Le document souligne que les principaux obstacles au compostage sont le manque d’espace et d’initiatives locales. Cependant, ces chiffres, datant de 2020, sont à nuancer en 2024, où les initiatives publiques se sont largement renforcées.Figure 3 : Étude sur l’information donné aux français
Le dernier document fait écho aux informations recueillies lors d’une interview avec un employé de la métropole de Brest. Ce dernier souligne que les citoyens utilisent souvent mal les composteurs collectifs en jetant des déchets non compostables comme la viande, ce qui pose plusieurs problèmes tels que l’apparition de nuisibles comme les rats. Cette mauvaise utilisation rend selon lui, nécessaire une maintenance accrue des composteurs.
B. Économique
La transition vers une économie circulaire et la prise de conscience croissante des enjeux environnementaux incitent de plus en plus de consommateurs et d’entreprises à explorer des solutions de compostage. Cette tendance offre un potentiel considérable pour transformer les déchets organiques en ressources précieuses, tout en soutenant des pratiques durables.
Tendance vers l’économie circulaire
L’économie circulaire est un modèle économique qui vise à réduire le gaspillage et à optimiser l’utilisation des ressources. Le compostage s’inscrit parfaitement dans cette dynamique en valorisant les biodéchets pour enrichir le sol et réduire l’impact environnemental. [13]
Retour sur investissement (ROI)
- Argument marketing : L’eau souillée produite lors de la fermentation du compost peut devenir un atout marketing.
Émergence de startups
Plusieurs startups se lancent dans ce secteur de niche, développant des solutions comme des broyeurs pour réduire la taille du compost et des systèmes de collecte d’eaux souillées. Certaines entreprises intègrent des designs esthétiques pour rendre les solutions de compostage plus attrayantes, favorisant ainsi leur adoption. Par exemple, la startup Ceercle propose des composteurs fabriqués en terre cuite [14]. Cette dernière utilise la technique du lombricompostage pour décomposer les aliments domestiques. Nous avons identifié une autre entreprise nommée Greenzy qui propose à la vente des composteurs design et haut de gamme. [15]
- Innovations sur le marché : Plusieurs startups se lancent dans ce secteur de niche, développant des solutions comme des broyeurs pour réduire la taille du compost et des systèmes de collecte d’eaux souillées.
- Esthétique et fonctionnalité : Certaines entreprises intègrent des designs esthétiques pour rendre les solutions de compostage plus attrayantes, favorisant ainsi leur adoption. [16]
Coûts des composteurs
Le coût des composteurs reste relativement élevé, en raison des matériaux coûteux et du faible volume de ventes. Ce coût initial peut représenter un obstacle, en particulier pour les ménages à revenu modeste, limitant ainsi l’adoption généralisée.
Les prix des composteurs sont très variables en fonction des techniques employées pour décomposer les aliments et du niveau de finition du produit. Pour avoir un ordre d’idée du prix, l’entrée de gamme de Ceercle est proposée au tarif de 159€ tandis que les produits de Greenzy sont affichés à près de 1000€.
Technologies avancées
- Capteurs et coûts supplémentaires : L’intégration de capteurs pour mesurer en temps réel l’état du compost augmente les coûts. Bien que ces technologies puissent améliorer l’efficacité, elles complexifient la viabilité économique des solutions.
Opportunités de marché
- Création de nouveaux modèles économiques : Le développement de plateformes en ligne pour partager et revendre du compost pourrait stimuler la demande.
- Soutien gouvernemental : Des subventions et des incitations fiscales pour l’achat de composteurs pourraient encourager davantage de citoyens à adopter le compostage.
- Marché du compost de qualité : Avec l’essor de l’agriculture durable, le compost de qualité pourrait devenir une ressource précieuse, justifiant des prix plus élevés.
- Éducation et sensibilisation : Investir dans des campagnes de sensibilisation pourrait accroître l’adoption du compostage et élargir le marché.
- Innovation technologique : L’intégration de composteurs intelligents offrant des données en temps réel pourrait améliorer l’efficacité et l’attrait du compostage.
En conclusion, l’économie circulaire et les pratiques de compostage représentent non seulement une réponse aux enjeux environnementaux actuels, mais également une opportunité économique à ne pas négliger. En développant des solutions innovantes et en surmontant les obstacles existants, le marché du compost peut se transformer en un secteur dynamique et lucratif, bénéficiant à la fois aux particuliers et à la planète.
E. Environnemental
La prise de conscience écologique mondiale continue d’alimenter une demande croissante pour des solutions durables, dont le compostage fait partie intégrante. Cette tendance est largement motivée par les préoccupations relatives à la gestion des déchets, la réduction de l’empreinte carbone et la lutte contre le changement climatique.
Réduction des émissions de gaz à effet de serre
Les décharges, en décomposant les déchets organiques, produisent du méthane, qui est 25 fois plus nocif que le CO2 pour le réchauffement climatique. L’augmentation du compostage, notamment au niveau domestique ou municipal, représente une solution immédiate pour limiter ces émissions. Par exemple, des villes comme San Francisco et Paris ont adopté des politiques de compostage obligatoires pour les déchets alimentaires, contribuant à réduire considérablement les déchets mis en décharge. [17]
Amélioration de la qualité des sols
Le compost est un amendement organique qui améliore la qualité des sols en augmentant leur capacité à retenir l’eau, réduisant ainsi l’érosion et l’épuisement des nutriments. En France, l’usage du compost est de plus en plus encouragé dans l’agriculture biologique, où il constitue une solution naturelle et durable face à la dégradation des sols liée à l’utilisation intensive d’engrais chimiques et à la monoculture. L’apport de matière organique par le compost favorise également la biodiversité microbienne dans les sols, ce qui est crucial pour maintenir des écosystèmes agricoles sains.
Réponse aux changements climatiques
Le compostage a un rôle clé dans la lutte contre le changement climatique en capturant et stockant du carbone dans le sol. Ce processus, appelé séquestration du carbone, aide à absorber le CO2 de l’atmosphère [18]. De plus, en favorisant des pratiques de compostage à grande échelle, nous pouvons réduire la demande pour des intrants énergivores comme les engrais synthétiques, qui nécessitent des processus de fabrication à forte intensité énergétique et contribuent à la déforestation et à l’appauvrissement des sols.
Problèmes environnementaux liés au compostage
Cependant, le compostage à grande échelle présente également des défis environnementaux, notamment la gestion des lixiviats, qui peuvent polluer les eaux souterraines s’ils ne sont pas correctement contrôlés. Les installations de compostage doivent être bien gérées pour éviter les nuisances telles que les mauvaises odeurs ou la prolifération de nuisibles, comme les rongeurs et les insectes. Des technologies plus avancées, comme les composteurs intelligents ou les systèmes de contrôle des émissions, commencent à être adoptées pour surmonter ces obstacles.
Potentiel de régénération des zones urbaines
Dans un contexte urbain, le compostage peut également jouer un rôle central dans la revitalisation des espaces verts. Plusieurs villes, à travers des projets de compostage collectif, encouragent la réutilisation des déchets alimentaires pour enrichir les sols urbains et soutenir des initiatives de jardinage communautaire. Cela contribue non seulement à réduire la pression sur les systèmes d’élimination des déchets, mais aussi à promouvoir une meilleure résilience environnementale dans les villes.
En somme, le compostage permet de détourner une quantité significative de déchets organiques des décharges, où leur décomposition génère des émissions de méthane, un gaz à effet de serre extrêmement puissant. En transformant ces déchets en matière organique réutilisable pour l’agriculture et le jardinage, le compostage offre une alternative écologique en réduisant les besoins en engrais chimiques et en contribuant à l’amélioration de la santé des sols.
F. Légal
Depuis le 1er janvier 2024, le tri des biodéchets est devenu obligatoire pour tous les particuliers et professionnels en France, conformément à la loi anti-gaspillage pour une économie circulaire du 10 février 2020 [19]. Cette loi impose à chaque ménage de disposer d’une solution de collecte des restes alimentaires afin de valoriser les biodéchets. Les appartements, tout comme les maisons, sont concernés par cette obligation de tri à la source, rendant cette mesure applicable à l’ensemble de la population. [20].
Les collectivités locales ont la responsabilité de mettre à disposition des citoyens les moyens nécessaires pour le tri à la source des biodéchets [19]. Cela inclut la mise en place de systèmes de collecte séparée des biodéchets, qui peuvent être compostés sur place ou via une filière de valorisation externe. Le non-respect de ces obligations peut entraîner des sanctions administratives et financières [20].
En cas de non-respect des consignes pour le tri des déchets organiques, une amende forfaitaire de 35 euros peut être appliquée, majorée à 75 euros en cas de récidive [20]. Les copropriétés doivent également se conformer à ces réglementations, en mettant en place un système de collecte et en désignant un référent « compostage » [21].
L’arrivée de nouvelles réglementations concernant la gestion des déchets alimentaires joue donc un rôle déterminant dans l’évolution du marché. Cette approche pourrait, d’une part, encourager les particuliers à participer activement à la valorisation des déchets en compostant chez eux, ou d’autre part, inciter à une gestion centralisée par la municipalité pour optimiser la production d’énergie renouvelable à partir de la méthanisation des déchets.
Les entreprises du secteur doivent également prendre en compte ces évolutions législatives, car elles pourront être amenées à mettre en place des dispositifs de compostage au sein de leurs locaux, renforçant ainsi leur responsabilité sociétale. Les normes de qualité pour le compost, définies par des règlements tels que la norme NF U 44-051, garantissent que le compost produit respecte des critères de sécurité et de qualité, ce qui est essentiel pour sa valorisation en agriculture. [22]
III. Impact de l’étude sur notre problème initial
Au cours de notre étude, nous avons rencontré un dilemme concernant le choix des personas à privilégier. Nous avons identifié trois groupes clés :
- Les restaurateurs
- Les collectivités et les gestionnaires de logistique
- Les citadins, qui manifestent un véritable intérêt pour le compostage
Après une analyse approfondie, notre choix s’est porté sur les citadins. Nous avons constaté que les problématiques rencontrées par les collectivités et les gestionnaires de logistique étaient déjà bien établies et mieux rodées, tandis que les défis auxquels font face les restaurateurs nous ont paru trop complexes à traiter dans le cadre de notre étude. En effet, le nombre de repas servis en restauration et ceux préparés à domicile étant équivalents, il est difficile d’imposer des dispositifs de compostage sans une volonté claire de la part des restaurateurs et des gestionnaires.
De plus, nos entretiens avec des restaurateurs ont révélé qu’ils n’avaient pas d’incitation à mettre en œuvre des pratiques de compostage, sauf si cela était accompagné d’une incitation commerciale tangible. Cette incitation pourrait prendre la forme d’une valorisation réelle du compost, mais cette option semble limitée et nécessiterait un travail considérable pour établir un modèle économique viable, surtout en milieu urbain. Nous pensons qu’il serait plus approprié que l’État intervienne, par exemple, en proposant des réductions de charges pour les établissements qui compostent, si l’État estime que cela représente une solution viable. Cependant, il convient de noter qu’un flou juridique plane encore sur ce sujet.
En conclusion, nous avons décidé de nous concentrer sur les ménages. Ce choix est renforcé par le fait que ce marché est déjà établi et présente un potentiel non exploité, ainsi que des opportunités d’innovation. Nous nous sommes également interrogés sur les raisons pour lesquelles le compost de qualité est souvent perçu comme cher, ce qui pourrait être une piste d’exploration pour nos recherches futures.
IV. Bibliographie
[1] Ministère de la Transition écologique et de la Cohésion des territoires, « Les déchets alimentaires en France et dans l’Union européenne en 2021 », [En ligne]. Disponible : https://www.statistiques.developpement-durable.gouv.fr/les-dechets-alimentaires-en-france-et-dans-lunion-europeenne-en-2021?rubrique=&dossier=1028250. [Accédé : 06-oct-2024].
[2] Légifrance, « Loi n° 2021-1484 du 15 octobre 2021 portant lutte contre le gaspillage et économie circulaire », [En ligne]. Disponible : https://www.legifrance.gouv.fr/jorf/id/JORFTEXT000032036289/ . [Accédé : 06-oct-2024].
[3] Place du Pro, « Tri des biodéchets : exigences et solutions », [En ligne]. Disponible : https://www.placedupro.com/articles/2310/tri-des-biodechets-exigences-et-solutions-. [Accédé : 06-oct-2024].
[4] Zero Waste France, « Évaluation de la loi AGEC : quel bilan pour la réduction des déchets ? », [En ligne]. Disponible : https://www.zerowastefrance.org/publication/evaluation-de-la-loi-agec-quel-bilan-pour-la-reduction-des-dechets/. [Accédé : 06-oct-2024].
[5] Ministère de l’Économie, des Finances et de la Souveraineté industrielle et numérique, « Interdiction du plastique à usage unique », [En ligne]. Disponible : https://www.economie.gouv.fr/cedef/interdiction-plastique-usage-unique. [Accédé : 06-oct-2024].
[6] Ville de Brest, « Demander un composteur », [En ligne]. Disponible : https://brest.fr/gerer-mon-quotidien/dechets/demander-un-composteur#:~:text=Le%20compostage%20individuel%20permet%20de,composteurs%20adapt%C3%A9s%20%C3%A0%20vos%20besoins. [Accédé : 06-oct-2024].
[7] Ouest-France, « 400 abris-bacs pour le tri des biodéchets vont être installés dans la métropole brestoise d’ici 2025 », [En ligne]. Disponible : https://www.ouest-france.fr/bretagne/brest-29200/400-abris-bacs-pour-le-tri-des-biodechets-vont-etre-installes-dans-la-metropole-brestoise-dici-2025-9c581e1a-89e0-11ee-a92a-0b4bc05f91ae. [Accédé : 06-oct-2024].
[8] Ville de Brest, « Déchets alimentaires : un atout au menu », [En ligne]. Disponible : https://brest.fr/dechets-alimentaires-un-atout-au-menu. [Accédé : 06-oct-2024].
[9] CEER, « Composteur de cuisine », [En ligne]. Disponible : https://ceercle.eu/boutique/composteur-de-cuisine/?_gl=1*3c7ttu*_up*MQ..&gclid=Cj0KCQj. [Accédé : 06-oct-2024].
[10] Greenzy, « Le produit », [En ligne]. Disponible : https://greenzy.eu/le-produit/. [Accédé : 06-oct-2024].
[11] SPHERE, « Étude compostage : Rapport National 2020 », [En ligne]. Disponible : https://www.sphere.eu/wp-content/uploads/2020/09/SPHERE-OpinionWay-Etude_compostage-Rapport-National-2020.pdf. [Accédé : 06-oct-2024].
[12] Annonces Landaises, « Biodechets : place au tri à la source », [En ligne]. Disponible : https://www.annonces-landaises.com/actualites/biodechets-place-au-tri-a-la-source/. [Accédé : 06-oct-2024].
[13] Circulab, « Composting: a key to circular economy », [En ligne]. Disponible : https://circulab.com/fr/composting-a-key-to-circular-economy-2/#:~:text=Focus%20sur%20le%20compostage,%26%20d%C3%A9cryptage%20des%20solutions. [Accédé : 06-oct-2024].
[14] Ceercle, « Composteur design d’intérieur comme extérieur », [En ligne]. Disponible : https://ceercle.eu/ [Accédé : 24-oct-2024]
[15] Greenzy, « Composteurs design d’intérieur comme extérieur – Ceercle », [En ligne]. Disponible : https://greenzy.eu/?lang=fr%2F [Accédé : 24-oct-2024]
[16] Place du Pro, « Des innovations pour traiter les biodéchets », [En ligne]. Disponible : https://www.placedupro.com/articles/2402/des-innovations-pour-traiter-les-biodechets#:~:text=D%C3%A9couvrez%20comment%20exposer%20vos%20produits%20sur%20notre. [Accédé : 06-oct-2024].
[17] MerciSF, « San Francisco : la pionnière du compostage urbain exporte ses méthodes en France », [En ligne]. Disponible : https://mercisf.com/fr/2024/01/18/san-francisco-la-pionniere-du-compostage-urbain-exporte-ses-methodes-en-france/#:~:text=San%20Francisco%20a%20adopt%C3%A9%20une,de%20recyclage%20et%20de%20compostage.&text=outils%20pour%20les%20b%C3%A2timents%20commerciaux. [Accédé : 06-oct-2024].
[18] Zero Waste France, « Compost : améliorer la séquestration du carbone dans les sols non cultivés », [En ligne]. Disponible : https://www.zerowastefrance.org/compost-ameliorer-sequestration-carbone-sols-non-cultives/. [Accédé : 06-oct-2024].
[19] Composteur Citizen, « Compostage obligatoire », [En ligne]. Disponible : https://composteurcitizen.fr/compostage-obligatoire/#:~:text=Depuis%20le%201er%20janvier,pouvoir%20trier%20leurs%20d%C3%A9chets. [Accédé : 06-oct-2024].
[20] Syndic One, « Le compostage en copropriété : obligatoire », [En ligne]. Disponible : https://www.syndic-one.com/blog/lois-et-reglementation/le-compostage-en-copropriete-obligatoire/#:~:text=La%20loi%20ne%20limite,du%20tri%20%C3%A0%20la. [Accédé : 06-oct-2024].
[21] Cotoit, « Compostage obligatoire en copropriété », [En ligne]. Disponible : https://www.cotoit.fr/blog/compostage-obligatoire-copropriete/#:~:text=Dans%20le%20cadre%20de,anti%2Dgaspillage%20pour%20une%20%C3%A9conomie. [Accédé : 06-oct-2024].
[22] Inovalys, « Compost et amendements organiques selon la norme NF U44-051 », [En ligne]. Disponible : https://www.inovalys.fr/analyses/environnement/matieres-fertilisantes-et-support-de-cultures-mfsc/composts-amendements-organiques-selon-la-norme-nf-u44-051-statut-produit. [Accédé : 06-oct-2024].
[23] EconomieGouv, « Tri à la source des biodéchets : une nouvelle obligation, de nombreuses solutions | Ministère du Partenariat avec les territoires et de la Décentralisation Ministère de la Transition écologique, de l’Énergie, du Climat et de la Prévention des risques Ministère du Logement et de la Rénovation urbaine », [En ligne]. Disponible : https://www.ecologie.gouv.fr/biodechets [Accédé : 24-oct-2024]
STOPCAR – État de l’art
Etat de l’art du projet : STOPCAR
par Antoine VIOLLEAU Eliot WALTER Nantenin Sibidé Kliser Javier REYES Amaury Bernardin
Introduction
Le constat est clair : nos modes de déplacement actuels ne sont pas soutenables à long terme, tant d’un point de vue environnemental qu’économique. Si 75% [4] de l’énergie consommée par nos voitures sert à transporter des sièges vides, cela met en lumière l’inefficacité de l’autosolisme. Pourtant, ce mode de déplacement reste largement préféré, malgré les alternatives qui se développent, tant sur le plan des transports en commun que des solutions de mobilité partagée ou douce. Mais pourquoi ?
C’est un fait : la voiture individuelle apporte un confort et une liberté auxquels beaucoup de citoyens restent attachés. Cependant, cette liberté a un coût élevé, non seulement pour l’environnement, mais aussi pour la collectivité, en termes de congestion urbaine, de pollution de l’air et d’émissions de gaz à effet de serre. L’autosolisme, défini comme l’utilisation individuelle de la voiture sans passager, incarne cette contradiction. Nous avons pris l’habitude de nous déplacer seuls dans des véhicules conçus pour transporter plusieurs personnes, entraînant une utilisation disproportionnée des ressources énergétiques.
Un enjeu environnemental et humain
Face à ces défis, la question se pose : comment encourager un changement de comportement ? Ce n’est pas seulement une question de technologie ou d’infrastructure, mais aussi une question de choix individuels, de perception du confort, et d’adaptation à des solutions alternatives. De plus, il faut comprendre si ces alternatives sont réellement accessibles à tous. En milieu urbain, les transports en commun ou les mobilités douces, comme le vélo, semblent offrir des solutions viables, mais qu’en est-il dans les zones périurbaines ou rurales ?
Les politiques publiques, quant à elles, semblent avancer lentement sur ce sujet, malgré l’urgence climatique. Les objectifs ambitieux, tels que la réduction des émissions de CO2 ou la transition vers des villes plus durables, semblent parfois déconnectés des réalités quotidiennes des citoyens.
Des solutions à portée de main ?
Dans ce contexte, quelles sont les solutions concrètes qui pourraient être mises en œuvre pour réduire l’autosolisme et encourager des pratiques de mobilité plus durables ? Les initiatives de covoiturage, les politiques favorisant les transports en commun ou encore les infrastructures dédiées à la mobilité douce sont-elles suffisantes ? Ou bien est-ce la perception même du déplacement qui doit être profondément transformée ?
Acteurs Concernés
Dans l’autosolisme, on peut distinguer d’autres acteurs au-delà du conducteur et passager. En effet ces deux profils sont des utilisateurs mais interviennent dans ce domaine :
- utilisateurs,
- organismes publiques (métroples, départements…);
- entreprises privées (opérateurs de transport publics, comité d’entreprises privés..);
- associations (Alliance pour la Décarbonisation de la Route,…).
Par exemple, les départements ou régions mettent en place des aides pour favoriser la multimodalité. Cela peut aussi être le cas des établissements publics, comme à l’IMT Atlantique ou des vélos et trottinettes électriques (chargé via panneaux solaires) sont à disposition du personnel et des étudiants.
Les entreprises peuvent prendre des mesures en internet, et pour les entreprises spécialisées dans le domaine du transport, des partenariats existent pour faciliter la multimodalité. Par exemple, en région parisienne, deux trajets/jour de BlablaCar Daily sont inclus dans le forfait transport en commun Navigo.
Interactions Observées
Les enquêtes de terrain ont permis de mettre en lumière différentes interactions entre les acteurs concernés par l’autosolisme. Par exemple, les autorités locales tentent d’encourager l’usage de modes de transport alternatifs comme le covoiturage ou les transports en commun en proposant des aides financières et des infrastructures adaptées. Toutefois, la majorité des usagers continuent de privilégier l’usage individuel de la voiture.
Par ailleurs, les entreprises jouent également un rôle clé dans cette dynamique en facilitant l’adoption de solutions multimodales pour leurs employés, mais ces initiatives peinent parfois à concurrencer le confort perçu de l’autosolisme.Les associations, de leur côté, sensibilisent sur les impacts environnementaux et économiques de cette pratique, en favorisant des alternatives plus durables comme le covoiturage, le vélo ou les transports partagés.
Ces multiples interactions révèlent une volonté collective d’agir contre l’autosolisme, mais elles sont encore confrontées à des résistances comportementales fortes.
Liens avec les scénarios de l’ADEME
L’ADEME est un vecteur important de massification des solutions et de mobilisation des acteurs dans un objectif de transition écologique. À ce titre, il dispose de plusieurs leviers de financement. À travers le Fonds Chaleur renouvelable, le Fonds Économie circulaire et le Fonds Air-mobilité, ils financent toutes les étapes, de la recherche au développement jusqu’à l’industrialisation d’une solution. En ayant pris contact avec eux, ils incitent des types de projets comme le nôtre à déposer des dossiers de candidature complets sur leur site, notre projet rentre en ligne de compte comme action de prévention. Détenue à 100 % par l’État et intégrée dans le plan « France 2030 », ADEME Investissement est une structure dont la mission est de financer en fonds propres des projets innovants d’infrastructures dans le domaine de la transition énergétique et écologique aux côtés d’acteurs privés. Elle est dotée d’une enveloppe de 400 millions d’euros.
Recherche documentaire
En 2017, VINCI Autoroutes a présenté les résultats de sa troisième campagne destinée à analyser les pratiques de partage de véhicules entre les Français. Cette campagne comprenait une enquête de terrain réalisée auprès de 668 utilisateurs des parkings partagés de son réseau, ainsi qu’une enquête d’opinion menée par Ipsos auprès de 2 192 Français. Ces données permettent d’obtenir une vision plus claire des tendances et des comportements liés au covoiturage dans le pays.
Dans l’infographie suivante, il est souligné que 81 % des déplacements en covoiturage sont liés à des activités professionnelles. Ce chiffre met en lumière l’importance du partage de véhicules dans le contexte professionnel en France. De plus, les raisons spécifiques de ces déplacements sont détaillées. Ces résultats reflètent comment le covoiturage est devenu une solution pratique et efficace pour les besoins de mobilité des travailleurs.
Figure 1. Répartition des déplacements en covoiturage selon l’activité professionnelle en France. [13]
Voici les raisons pour lesquelles les Français optent pour le covoiturage. Ces raisons soulignent non seulement les avantages économiques, mais aussi l’importance de la convivialité et l’impact positif sur l’environnement.
Figure 2. Motivations des Français pour utiliser le covoiturage. [13]
La prochaine infographie révèle que le covoiturage est une option de transport particulièrement populaire parmi les personnes vivant en dehors des villes, où l’accès aux transports publics peut être limité. De plus, la tendance vers le partage de véhicules dans ces zones pourrait contribuer à améliorer la mobilité et à réduire la congestion dans les zones urbaines. Ces résultats soulignent la pertinence du covoiturage en tant que solution de transport durable et efficace pour diverses communautés.
Figure 3. Répartition géographique des covoitureurs en France. [13]
La suivante image illustre les alternatives de transport que les covoitureurs utiliseraient s’ils n’avaient pas accès au covoiturage. Les résultats indiquent qu’une grande majorité (85 %) continuerait à opter pour l’utilisation de la voiture, ce qui souligne l’importance du covoiturage comme une alternative viable pour réduire la dépendance au transport individuel. De plus, seul un petit pourcentage envisagerait d’autres formes de transport, comme le train (8 %), la moto ou les transports en commun (2 %). Cette analyse met en lumière la nécessité de promouvoir des solutions de mobilité partagée pour décourager l’utilisation exclusive de la voiture.
Figure 4. Modes de transport alternatifs en l’absence de covoiturage.
Évolution du covoiturage (carpooling)
Environ 40 000 déplacements par jour sont réalisés par les plateformes de mises en relations. Bien qu’ils ne représentent que 4% des trajets covoiturés chaque jour, les plateformes multiplient la capacité des personnes à covoiturer pour chacun de leurs trajets, en dehors de leur cercle de connaissance. Le nombre de trajets réalisés chaque jour sur une plateforme peut être suivi chaque jour grâce au registre de preuve de covoiturage auquel sont connectées 26 plateformes.Le registre de preuve RPC collecte et certifie les données des trajets de covoiturage courte distance intermédiaire. Les données qui sont collectées sur le Registre permettent ensuite aux collectivités et plus largement à l’ensemble des acteurs de l’écosystème du covoiturage d’inciter et de développer en toute confiance la pratique sur leur territoire sur la base de données réelles vérifiées. 26 plateforme en son partenaire et contribue à l’élaboration de suivi du registre.
Figure 5. Évolution du nombre mensuel de trajets quotidiens via les plateformes de covoiturage. [5]
Données clés
Les données suivantes ont été obtenues à partir de l’enquête « Mobilité des personnes » de 2018-2019 [19]. Cette enquête fait partie des enquêtes nationales sur les déplacements des personnes, réalisées tous les dix ans. Elle constitue une source d’information unique et incontournable dans les statistiques sur la mobilité, permettant de mesurer les évolutions.
Figure 6. Trajets en voiture. Seul, à plusieurs ou en covoiturage ? [18]
Cette enquête a également permis de connaître l’occupation des voitures en fonction de la distance du déplacement et des motifs de ces déplacements en 2019.
Figure 7. Occupation des voitures selon la distance du déplacement en 2019 (en %). [18]
Figure 8. Occupation des voitures selon le motif du déplacement en 2019 (en %). [18]
Eco-système visé
Politiques
En ce qui concerne les facteurs politiques influençant le covoiturage en France, l’écosystème est façonné par divers soutiens gouvernementaux visant à encourager et réguler ce mode de transport partagé.
Investissement financier du gouvernement
- Depuis le 1er janvier 2023, le gouvernement français offre une prime de 100 euros aux conducteurs qui effectuent des trajets partagés de courte distance. La prime est reversée par les plateformes de covoiturage, sous la forme d’un versement progressif : une première partie au premier covoiturage (minimum 25 €) et le reste au dixième covoiturage, dans un délai de 3 mois à compter de son premier covoiturage [4].
Certaines plateformes de covoiturage compatibles avec la prime de 100 € : BlaBlaCarDaily, Coivoit’ici, Covoiturage-leman.org, Coopgo, Ecov, Lane.
- Loi d’Orientation des Mobilités (LOM) : Cette loi a impliqué un investissement de 13,4 milliards d’euros pendant la période 2017-2022 pour donner la priorité aux transports quotidiens. De plus, elle encourage les entreprises et les autorités locales à promouvoir l’usage partagé des véhicules [1].
- Le gouvernement et les entrepreneurs, grâce au paquet de mobilité durable (FMD), encouragent l’utilisation d’une mobilité moins polluante [1].
Les employés du secteur privé peuvent bénéficier d’une DMF allant jusqu’à 800 €/an, exonérée de l’impôt sur le revenu. Ce soutien optionnel, payé par l’employeur, est exempt de cotisations et de charges sociales pour eux. Les agents du secteur public bénéficient d’un paquet de mobilité durable de 300 € qu’ils peuvent combiner avec le remboursement de l’abonnement de transport public.
Economiques
1.Coût financier du carburant et des véhicules
- Fluctuations des prix du carburant : L’un des principaux facteurs économiques qui influence le choix de la voiture individuelle est le prix du carburant. En période de hausse des prix du pétrole, de nombreux ménages ressentent une pression financière accrue, ce qui peut les inciter à envisager des solutions de transport alternatives, comme le covoiturage ou les transports en commun. À l’inverse, lorsque les prix du carburant sont bas, l’incitation à abandonner la voiture individuelle diminue.
- Coût d’achat et d’entretien des véhicules : L’acquisition et l’entretien d’une voiture individuelle représentent un investissement financier conséquent (achat, assurance, réparations, stationnement, etc). L’usage de la voiture entraîne aussi des coûts liés à l’usure des routes et aux infrastructures (parking, entretien des routes), qui sont majoritairement financés par les contribuables.
2.Subventions et incitations financières
Cette partie a déjà été traitée sur l’analyse politique étant donné que la majeure partie des dispositifs font suite à un travail gouvernemental.
3.Le coût des alternatives à la voiture individuelle
- Prix des transports en commun : Le coût des transports en commun est un facteur déterminant dans le choix des modes de déplacement. Lorsque les tarifs sont abordables et les services efficaces, les citoyens peuvent être incités à abandonner leur voiture individuelle. Ce n’est pas toujours le cas, mais on retrouve régulièrement des tarifs destinés aux ménages modestes. Ce qui devrait être un facteur positif pour ces personnes, qui ne sont peut être pas véhiculées.
- Investissements publics dans les infrastructures : Les politiques publiques orientées vers la construction d’infrastructures de transport en commun, de pistes cyclables ou d’aménagements pour la mobilité douce sont souvent dictées par des considérations économiques. Plus les investissements dans ces infrastructures augmentent, plus l’offre de solutions alternatives devient attractive pour les usagers.
4.Le coût pour la société
- Coûts externes de la pollution et des embouteillages : L’usage massif de la voiture individuelle engendre des coûts externes importants pour la société, tels que les frais liés à la pollution atmosphérique, les maladies associées à cette pollution, ou encore le temps perdu dans les embouteillages. Ces coûts cachés ne sont pas directement pris en compte par les utilisateurs de voitures individuelles, mais ils pèsent lourdement sur les finances publiques.
- Coût de la congestion urbaine : Dans les grandes villes, l’autosolisme contribue de manière significative aux embouteillages, qui à leur tour augmentent les coûts économiques pour les entreprises (livraisons retardées, productivité réduite) et les particuliers (temps perdu, stress). La gestion de ces externalités économiques devient un enjeu clé pour les décideurs publics.
En conclusion, l’analyse économique de l’autosolisme met en lumière des coûts directs et indirects importants pour les usagers et la société dans son ensemble. La transition vers des modes de transport plus durables nécessitera non seulement des investissements publics, mais aussi et surtout une prise de conscience des coûts réels associés à l’utilisation individuelle de la voiture, tant en termes financiers que environnementaux.
Sociologiques
L’autosolisme, c’est-à -dire rouler seul en voiture va à l’encontre des enjeux sociaux. C’est une pratique qui favorise le confort individuel au dépend des conséquences sociales et environnementales.
1.Isolement et inégalité social :
L’autosolisme est favorisé dans les zones rurales et périurbaines. Dans ces zones la voiture est souvent le seul moyen de se déplacer efficacement, ce qui peut renforcer la dépendance à la voiture et isoler les personnes sans véhicule. Ce phénomène accentue les inégalités dans ces zones car crée une scission pour les personnes n’ayant pas les moyens d’acheter, d’entretenir et de conduire une voiture. Notamment les jeunes, les personnes âgées ou les personnes handicapées qui n’ont pas d’accès facile à une voiture.
2.Surcharge des infrastructures urbaines :
Le nombre élevé de voitures individuelles sur la route entraîne une congestion des routes, causant des embouteillages qui affectent la qualité de vie des citadins et augmentent les temps de trajet. En outre, augmenter les infrastructures pour les voitures est une solution contre-productive pour décongestionner les axes existants. Pour cela nous pouvons citer l’exemple de Katy Freeway. Il s’agit de l’autoroute la plus large au monde à Houston, USA. Ce projet faramineux à 2,8 milliards de dollars a abouti à 26 voies d’autoroutes, 13 voies par sens. Le but était d’augmenter la capacité de l’autoroute pour fluidifier le trafic. Mais depuis la construction des nouvelles voies, le trafic n’a cessé de se dégrader : +30 à 55% de temps de trajet en plus. [21]
3.Répercussion sur la santé :
Une étude de 2021 de Santé Publique France montre que la pollution liée aux transports serait responsable de 48 000 décès prématurés par an en France. Santé Public France propose la réduction de l’autosolisme comme une des solutions majeures pour diminuer cette mortalité.
D’un autre côté, l’Institut National de la Santé et de la Recherche Médicale (INSERM) à montré dans son rapport de 2016 l’impact des trajets domicile-travail sur la santé mentale. Notamment l’augmentation de l’anxiété, la dépression et le stress chronique. [20]
4.Implication écologique :
La réduction de l’autosolime en appelle à la responsabilité collective de chacun car le recours excessif à la voiture individuelle contribue à l’augmentation des émissions de gaz à effet de serre. Cette même responsabilité collective pourrait pousser à utiliser des alternatives plus durables comme le covoiturage, l’auto stop, ou les transports en commun.Selon l’Agence de l’environnement et de la maîtrise de l’énergie (ADEME), un trajet en voiture émet en moyenne 200 g de CO₂ par kilomètre parcouru. En covoiturant à quatre personnes, cette empreinte carbone est divisée par autant de passagers, ramenant l’émission individuelle à environ 50 g de CO₂ par kilomètre. Cela représente une réduction de 75 % par personne, comparé à un trajet effectué seul en voiture. Si chaque conducteur habituel partageait ses trajets avec trois passagers, cela permettrait d’éviter l’émission de plusieurs tonnes de CO₂ chaque année.
Technologiques
Il existe de nombreuses manières possibles qui permettent de mettre en relation des personnes se rendant d’un même point A en passant par un même point B. L’art serait d’y parvenir aujourd’hui dans un contexte de réduction maximale de l’utilisation de l’énergie, ainsi de le réaliser en utilisant la solution la plus lowtech possible.
Le terme low-tech est utilisé pour qualifier des objets, des systèmes, des techniques, des services, des savoir-faire, des pratiques, des modes de vie et même des courants de pensée, qui intègrent la technologie selon trois grands principes. 1- Utile : Une low-tech répond à des besoins essentiels à l’individu ou au collectif. Elle contribue à rendre possible des modes de vie, de production et de consommation sains et pertinents pour tous dans des domaines. 2- Accessible: La low-tech doit être applicable par le plus grand nombre. Elle doit donc pouvoir être fabriquée et/ou réparées localement, ses principes de fonctionnement doivent pouvoir être appréhendés simplement et son coût adapté à une large part de la population. 3- Durable : Éco-conçue, résiliente, robuste, réparable, recyclable, agile, fonctionnelle : la low-tech invite à réfléchir et optimiser les impacts tant écologiques que sociaux ou sociétaux liés au recours à la technique .
Dans une perspective low-tech, il est possible d’utiliser des outils déjà existants en leur ajoutant des fonctionnalités supplémentaires. Nous avons pensé, notamment, à la technologie de Waze qui permet de géolocaliser en temps réel l’ensemble de ses utilisateurs. Utiliser l’API de Waze ou négocier avec eux pour ajouter une fonctionnalité spécifique est une solution low-tech envisageable. Nous avons également envisagé un formulaire à remplir, similaire à celui de Blablacar Daily, avec dans notre cas l’ajout de bornes connectées à des points stratégiques de la ville.
L’idée que nous voulons conserver est le spontané/ l’instantané ainsi cela nécessite des technologie web avancé permettant de notifier l’utilisateur en temps réel.
Environnementaux
La réduction des gaz à effet de serre (GES) est une préoccupation majeure, car près d’un quart des émissions de CO₂ de l’Union Européenne provient du transport routier. De plus, plus de 80 % des trajets sont effectués par une seule personne. Notre objectif est donc de réduire l’autosolisme, ce qui aura plusieurs effets bénéfiques :
- Diminuer le nombre de véhicules sur les routes,
- Réduire les embouteillages,
- Par conséquent, diminuer les émissions de CO₂ par personne,
- Améliorer la qualité de l’air et donc le cadre de vie global.
La diminution de l’autosolisme contribue également à la conservation des ressources rares comme l’essence, ce qui réduit l’impact environnemental lié à l’extraction et au transport des combustibles fossiles. En partageant les véhicules, nous limitons aussi la nécessité de fabriquer de nouveaux véhicules, ce qui préserve davantage de ressources et réduit l’empreinte écologique de leur production.
Au-delà des avantages environnementaux directs, il y a également des bénéfices pour la qualité de vie des citoyens. Une réduction du nombre de voitures sur les routes entraînera :
- Moins de nuisances sonores,
- Moins de congestion et donc une circulation plus fluide,
- Un cadre de vie amélioré dans les zones urbaines.
À long terme, cette diminution de l’autosolisme permettra d’optimiser les infrastructures de transport de manière plus durable. Avec moins de voitures sur les routes, les parkings pourront être réduits en taille, les routes moins souvent élargies ou reconstruites, et l’on pourra investir davantage dans des modes de transport en commun comme les bus et les trains.
Notre objectif de réduire l’autosolisme vise également à changer les habitudes des citoyens et à favoriser des comportements plus respectueux de l’environnement. En promouvant ces nouvelles pratiques de mobilité durable, nous pourrons ensemble réduire l’impact environnemental global et adopter des tendances plus vertes pour un avenir plus durable.
Légaux
La réglementation de la circulation sur les voies de covoiturage repose sur la récente Loi d’Orientation des Mobilités (LOM) (votée le 24/12/2019), qui a modifié le Code de la route et le Code général des collectivités territoriales, pour donner la possibilité à l’autorité de police de la circulation de réserver une voie à la circulation, entre autres, aux véhicules transportant un nombre minimal d’occupants en particulier dans le cadre du covoiturage. [14]
1.Loi d’Orientation des Mobilités : La LOI n° 2019-1428 du 24 décembre 2019 d’orientation des mobilités définit plusieurs mesures pour le covoiturage [15][1] :
- L’intégration du covoiturage parmi les leviers d’action des intercommunalités et des Régions. Elles peuvent dorénavant verser une allocation aux conducteurs et aux passagers dans le cadre de déplacements en covoiturage (subvention des trajets, défiscalisation de ces aides).
- L’inscription des questions de déplacements des travailleurs comme un des thèmes des négociations obligatoires à mener dans les entreprises de plus de 50 salariés sur un même site.
- L’accélération de la création de voies réservées sur les axes routiers structurants et facilitera le stationnement dédié au covoiturage.
- La création du forfait mobilités durables qui permet aux employeurs du secteur privé de prendre en charge jusqu’à 800 euros par an et par salarié les frais de déplacement de leurs salariés sur leur trajet domicile-travail effectué à vélo, en covoiturage ou à l’aide d’autres services de mobilité partagée (véhicules en autopartage, engins en free-floating…).
Cette loi vise à encourager des alternatives à l’utilisation individuelle de la voiture, à promouvoir une mobilité plus durable et à réduire l’empreinte carbone [11][17].
2.Code de la route: Selon l’article L411-8, l’autorité investie du pouvoir de police de la circulation peut, eu égard aux nécessités de la circulation ou de la protection de l’environnement, réglementer, de façon temporaire, notamment à certaines heures, ou de façon permanente, la circulation sur la voie publique du réseau routier national ou du réseau routier départemental hors agglomération.
Elle peut notamment réserver une partie de la voie publique pour en faire une voie de circulation destinée à faciliter la circulation des véhicules de transport en commun, des taxis, des véhicules transportant un nombre minimal d’occupants notamment dans le cadre du covoiturage au sens de l’article L. 3132-1 du code des transports ou des véhicules à très faibles émissions au sens de l’article L. 318-1 du présent code [2].
3.Code général des collectivités territoriales : Selon l’article L2213-3, le maire peut, par arrêté motivé :
Réserver des emplacements sur la voie publique, de façon permanente ou à certaines heures, pour faciliter la circulation des véhicules de transport en commun, des taxis, des véhicules transportant un nombre minimal d’occupants notamment dans le cadre du covoiturage au sens de l’article L. 3132-1 du code des transports ou des véhicules à très faibles émissions au sens de l’article L. 318-1 du code de la route [3].
4.Code des Transports : L3132-1 du code des transports définie le véhicule comme « l’utilisation en commun d’un véhicule terrestre à moteur par un conducteur et un ou plusieurs passagers, effectuée à titre non onéreux, excepté le partage des frais, dans le cadre d’un déplacement que le conducteur effectue pour son propre compte« . [16]
Quelles sont les techniques (ou produits) qui pourraient répondre partiellement ou complètement au problème ?
Pour répondre à la problématique de la réduction du nombre de voitures vides et de la création d’un climat de confiance entre conducteurs et passagers, plusieurs applications et techniques existent.
Par exemple, des applications comme BlaBlaCar ou Mobicoop facilitent le covoiturage longue distance en mettant en relation des utilisateurs vérifiés partageant des trajets similaires. Pour les trajets du quotidien, des solutions comme OuestGo dans l’Ouest de la France, ou encore BlaBlaCar Daily et Klaxit sont particulièrement adaptées aux trajets domicile-travail ou domicile-étude, souvent utilisés par les entreprises ou les campus universitaires. Ces services permettent d’établir des relations régulières, et un covoiturage informel peut même se poursuivre sans ces applications.
En parallèle, des solutions comme Ecov et RezoPouce apportent une réponse spécifique aux besoins des zones rurales et périurbaines, avec des lignes de covoiturage sans réservation. En collaboration avec les collectivités locales, ces plateformes installent des arrêts de covoiturage où les passagers renseignent leur destination via un panneau ou une application, et les conducteurs inscrits peuvent facilement les prendre en charge. Ce type de covoiturage solidaire ou à haut niveau de service permet de réduire efficacement l’autosolisme, tout en améliorant la mobilité locale et la qualité de vie.
Quelle est l’environnement règlementaire ?
Il n’existe pas de réglementation spécifique en France ou en Europe ciblant directement l’autosolisme (l’utilisation de la voiture par une seule personne), mais plusieurs initiatives, lois et régulations visent indirectement à réduire l’autosolisme en encourageant des alternatives plus durables, comme le covoiturage, les transports en commun, et les mobilités douces comme le vélo.Par exemple, dans son cadre du Plan Climat 2026-2030, la ville de Paris dédie depuis les Jeux Olympiques sur le périphérique réservé au covoiturage et au transport en commun. Les autosolistes sont verbalisés.
Conclusion et remise en question
Lorsque nous avons initialement réfléchi à une solution, l’accent a tout de suite été mis sur l’instantané et le spontanée. Nous étions dans une logique d’uberisation avec quelque chose de très simple à utiliser et surtout de donner une réponse très rapide au problème de mobilité. La réalité après étude de l’état de l’art de notre projet et que pour qu’une telle solution fonctionne et soit adoptée il faudrait une masse critique de personne soit utilisateur de la plateforme et pas seulement en piéton mais surtout en conducteur. Après avoir analysé la bibliographie du sujet et plus largement les solutions existantes il nous est apparu clairement que le problème ne manquait pas tant de solution viable mais plutôt de personne pour les promouvoir. Avec le fond ADEME nous pouvons obtenir des financements pour promouvoir le type de déplacement vert qu’est le covoiturage, aussi il serait bon d’avoir une solution qui favorise le covoiturage en mettant l’accent sur le problème que représente l’autosolisme.
Références bibliographiques
[1] Consulté le: 6 octobre 2024. [En ligne]. Disponible sur: https://www.ecologie.gouv.fr/loi-dorientation-des-mobilites
[2] « Article L411-8 – Code de la route – Légifrance ». Consulté le: 6 octobre 2024. [En ligne]. Disponible sur: https://www.legifrance.gouv.fr/codes/article_lc/LEGIARTI000039675126
[3]« Article L2213-3 – Code général des collectivités territoriales – Légifrance ». Consulté le: 6 octobre 2024. [En ligne]. Disponible sur: https://www.legifrance.gouv.fr/codes/article_lc/LEGIARTI000039787448/2019-12-27
[4]« Covoiturage : informations à connaître ». Consulté le: 6 octobre 2024. [En ligne]. Disponible sur: https://www.ecologie.gouv.fr/politiques-publiques/covoiturage-france-ses-avantages-reglementation-vigueur
[5]« Covoiturage du quotidien | Ministère du Partenariat avec les territoires et de la Décentralisation Ministère de la Transition écologique, de l’Énergie, du Climat et de la Prévention des risques Ministère du Logement et de la Rénovation urbaine ». Consulté le: 6 octobre 2024. [En ligne]. Disponible sur: https://www.ecologie.gouv.fr/covoiturage
[6]É. Pigalle, J.-B. Ray, et S. Godillon, « Entretien. Quelles perspectives pour le covoiturage en France ? », Flux, vol. 119120, no 1, p. 192‑196, juill. 2020, doi: 10.3917/flux1.119.0192.
[7]« Environnement : la voiture, un frein aux ambitions climatiques de la France ». Consulté le: 6 octobre 2024. [En ligne]. Disponible sur: https://www.lemonde.fr/planete/article/2021/12/02/environnement-la-voiture-un-frein-aux-ambitions-climatiques-de-la-france_6104418_3244.html
[8]« ID4Mobility | innovation & industrial mobility ecosystem ». Consulté le: 24 septembre 2024. [En ligne]. Disponible sur: https://www.id4mobility.org/
[9]M. TONNERRE, « Ils ne peuvent plus aller au Technopôle en bus en journée : à Brest, les usagers se mobilisent », Ouest-France.fr. Consulté le: 24 septembre 2024. [En ligne]. Disponible sur: https://www.ouest-france.fr/bretagne/brest-29200/ils-ne-peuvent-plus-aller-au-technopole-en-bus-en-journee-a-brest-les-usagers-se-mobilisent-020f35f0-4d95-11ee-90c9-6337e94e3b07
[10]N. Baron-Yellès, « La fabrique politique du covoiturage périurbain », Espaces et sociétés, vol. 188, no 1, p. 93‑111, avr. 2023, doi: 10.3917/esp.188.0093.
[11]« La loi d’orientation des mobilités | Ministère du Partenariat avec les territoires et de la Décentralisation Ministère de la Transition écologique, de l’Énergie, du Climat et de la Prévention des risques Ministère du Logement et de la Rénovation urbaine ». Consulté le: 6 octobre 2024. [En ligne]. Disponible sur: https://www.ecologie.gouv.fr/loi-dorientation-des-mobilites
[12]« Les Français et le covoiturage : l’enquête de VINCI Autoroutes ». Consulté le: 6 octobre 2024. [En ligne]. Disponible sur: https://corporate.vinci-autoroutes.com/fr/francais-covoiturage-lenquete-vinci-autoroutes
[13]A. Grasset, J. Sawtschuk, et T. Michot, « Les pratiques du vélo à l’Université de Bretagne-Occidentale (UBO) à Brest », Transports urbains, vol. 144, no 1, p. 15‑20, 2023.
[14]« Les voies réservées au covoiturage en France : un état des lieux du Cerema | Cerema ». Consulté le: 6 octobre 2024. [En ligne]. Disponible sur: http://www.cerema.fr/fr/actualites/voies-reservees-au-covoiturage-france-etat-lieux-du-cerema
[15]LOI n° 2019-1428 du 24 décembre 2019 d’orientation des mobilités (1). 2019.
[16]« Quels sont les droits et obligations des passagers en covoiturage ? » Consulté le: 6 octobre 2024. [En ligne]. Disponible sur: https://lemagdelaconso.ouest-france.fr/dossier-435-droits-obligations-passagers-covoiturage.html
[17]« Réglementation Mobilité », Plan national de covoiturage du quotidien. Consulté le: 6 octobre 2024. [En ligne]. Disponible sur: https://employeursprocovoiturage.ademe.fr/reglementation-mobilite/
[18]« Se déplacer en voiture : seul, à plusieurs ou en covoiturage ? », Données et études statistiques pour le changement climatique, l’énergie, l’environnement, le logement, et les transports. [En ligne]. Disponible sur: https://www.statistiques.developpement-durable.gouv.fr/se-deplacer-en-voiture-seul-plusieurs-ou-en-covoiturage-0
[19]“Mobilité des personnes” [En ligne]. Disponible sur : https://www.statistiques.developpement-durable.gouv.fr/enquete-sur-la-mobilite-des-personnes-2018-2019
[20] « Stress au travail et santé : situation chez les indépendants » [En ligne]. Disponible sur : https://inserm.hal.science/inserm-02102646/
[21] “L’autoroute la plus large du monde s’étant sur 26 voies”. [En ligne]. Disponible sur : https://marjolein-teepen.com/fr/lautoroute-la-plus-large-du-monde-setend-sur-26-voies/
Glyc’ami – État de l’art – Suivi facile de glycémie pour les séniors
État de l’art du projet Glyc’ami
par Clara AFONSO-OLIVEIRA | Tianjiao LIU | Hermann KOUAKOU | Sami BONNIN | Etienne ILIOU
V2 – 25 octobre 2024
Introduction
- Contexte général
En 2022, la France comptait plus de 4 millions de personnes touchées par le diabète, une maladie chronique dont la prévalence continue de grimper. Entre 2015 et 2022, cette prévalence est passée de 5,6 % à 6,3 %, illustrant une épidémie silencieuse qui s’étend chaque année. Cette évolution est symptomatique d’une crise de santé publique de grande ampleur, exacerbée par nos modes de vie actuels. Mais les habitudes alimentaires et le manque d’activité physique ne sont que la partie visible de l’iceberg.
Les statistiques révèlent que nous faisons face à un phénomène multifactoriel. Les conditions socio-économiques et environnementales, telles que la sédentarité accrue, la précarité alimentaire ou encore les inégalités d’accès aux soins, jouent un rôle déterminant dans cette explosion des cas de diabète. La question de la prise en charge de la maladie devient ainsi un enjeu central, tant pour le système de santé que pour les patients eux-mêmes.
Alors que les traitements et technologies de suivi progressent, le problème ne se limite plus aux seuls aspects médicaux. Il touche désormais à des questions plus larges de prévention et de soutien, avec un impératif : renforcer la sensibilisation et l’accompagnement des populations à risque.
Face à cette situation, il devient indispensable de repenser les dispositifs actuels et d’explorer de nouvelles solutions pour freiner cette progression.
Evolution de la population de diabétique de 2015 à 2022
source : federationdesdiabetiques.org
- Qu’est ce que le diabète ?
Le diabète est une maladie chronique liée à des problèmes de régulation de la glycémie (le taux de sucre dans le sang).
source : diabetesaguenaylacsaintjean.org
– Diabète de type 1
- Ce type est une maladie auto-immune qui touche environ 10 % des diabétiques [2].
- Il résulte de l’attaque par le système immunitaire des cellules productrices d’insuline dans le pancréas, entraînant une élévation dangereuse du taux de sucre dans le sang [4].
- Il est souvent diagnostiqué chez les jeunes, nécessitant un traitement par insuline quotidien.
– Diabète de type 2
- Représentant 90 % des cas, il est souvent lié à des facteurs de mode de vie tels que le surpoids, le manque d’activité physique et une alimentation déséquilibrée [2] [5].
- Ce diabète se manifeste lorsque le pancréas ne produit pas suffisamment d’insuline ou que les cellules du corps deviennent résistantes à celle-ci.
- Bien que plus fréquent chez les adultes, il peut également toucher des jeunes en surpoids, et son traitement repose sur des modifications du mode de vie, des médicaments oraux et, dans certains cas, de l’insuline.
En outre, le diabète gestationnel, qui touche 5 à 10 % des femmes pendant la grossesse, est souvent transitoire, disparaissant après l’accouchement [2].
Acteurs concernés et interactions observées :
Les interactions entre ces différents acteurs – patients, professionnels de santé, et le système de santé en général – soulignent les enjeux de sensibilisation, d’éducation thérapeutique et d’accès aux soins. La prise en charge du diabète nécessite donc une approche coordonnée et multi-facettes pour répondre aux défis que pose cette maladie chronique dans le paysage de la santé publique en France.
Un acteur pour lequel nous avons identifié de nombreuses difficultés à l’aide de nos recherches documentaires est la personne âgée diabétique de type 2.
Le diabète chez les personnes âgées, notamment le diabète de type 2, est particulièrement fréquent en France. Selon les données de la Société Francophone du Diabète et l’étude Entred 3, la majorité des patients atteints de diabète de type 2 ont en moyenne 67,6 ans [22]. Malheureusement, cette moyenne ne reflète pas la réalité puisqu’elle est tirée vers le bas en prenant en compte un nombre croissant de diabétiques de type 2 de moins de 55 ans. Des études montrent que l’incidence du diabète de type 2 est maximale entre 75 et 79 ans, avec 20 % des hommes et 14 % des femmes traités pour cette maladie [23].
Cette population est souvent touchée par des complications graves, telles que des maladies cardiovasculaires et rénales, et présente des facteurs de risque élevés comme l’hypertension et l’obésité. L’évolution du diabète chez les seniors exige un suivi médical rigoureux pour prévenir ces complications qui viennent souvent se superposer à d’autres problèmes de santé.
Chez les personnes âgées atteintes de diabète de type 2, les difficultés de la prise en charge de la maladie sont exacerbées par leur âge. Différentes études montrent les disparités dans la gestion du diabète en fonction de l’âge, et quatre grands critères sont souvent mis en avant.
- Déclin cognitif : Le diabète de type 2 accélère le déclin cognitif, affectant des fonctions comme la mémoire et la prise de décision. Cela rend la gestion du diabète plus difficile. Des études américaines montrent que l’hyperglycémie chronique affecte le cerveau et augmente le risque de démence [24]. Cela a un impact direct sur la capacité des seniors à suivre les traitements et les recommandations médicales.
- Isolement social : Les seniors diabétiques peuvent se retrouver socialement isolés en raison des complications physiques comme la neuropathie, qui réduit leur mobilité, mais aussi à cause de la fatigue générale liée à la maladie. Cet isolement aggrave leur bien-être mental et limite leur accès aux soins et au soutien social, essentiels pour une bonne gestion du diabète.
- Difficulté de compréhension de la maladie et du traitement : La complexité de la gestion du diabète (régime alimentaire, prise de médicaments, surveillance de la glycémie) devient plus difficile avec l’âge, notamment en raison des troubles cognitifs mentionnés précédemment. Cela conduit à une mauvaise adhésion thérapeutique, car les patients peuvent ne pas bien comprendre l’importance d’un suivi rigoureux ou les effets à long terme d’une gestion inadéquate [25].
- Fatigue liée à la prise pluriquotidienne de médicaments : La nécessité de prendre des médicaments plusieurs fois par jour (hypoglycémiants, insuline, etc.) crée une fatigue psychologique et physique. Les seniors expriment souvent une lassitude face à ces routines répétitives, ce qui peut entraîner des oublis ou un refus de suivre leur traitement correctement [26].
PESTEL
1. Facteurs Politiques
Les politiques de santé publique jouent un rôle majeur dans la gestion du diabète en France. Plusieurs aspects sont à considérer :
- Stratégies de santé publique [2] : Le gouvernement français met en place des campagnes de sensibilisation et des actions de dépistage, mais ces efforts sont parfois jugés insuffisants. Le Plan National Diabète 2014-2019 visait à améliorer la prise en charge des patients diabétiques, mais des critiques soulignent un besoin d’une politique de prévention plus agressive.
- Budget de la Sécurité Sociale [1] : Le diabète représente un coût élevé pour le système de santé français, avec un impact croissant dû à l’augmentation du nombre de cas. Les politiques de financement de la santé influencent donc directement la qualité des soins, l’accès aux technologies et les ressources disponibles pour la gestion de cette maladie.
- Réglementations sur les produits alimentaires : Les politiques de régulation sur la composition des aliments (sucre, graisse, etc.), ainsi que les taxes sur les boissons sucrées, influencent la prévention du diabète en s’attaquant à l’une de ses causes principales, à savoir une alimentation déséquilibrée.
2. Facteurs Économiques
L’analyse des facteurs économiques liés au diabète en France révèle des implications significatives tant pour les individus que pour la société, et remet en question notre problème initial en nous incitant à explorer des dimensions économiques plus larges :
- Coût des soins[1] : Nos entretiens ont mis en lumière des inégalités économiques importantes dans l’accès aux soins, en particulier concernant les nouvelles technologies comme les capteurs de glycémie et les pompes à insuline. Si ces dispositifs permettent une meilleure gestion du diabète, leur coût élevé et la lenteur de leur remboursement par l’Assurance Maladie freinent leur adoption, surtout chez les patients à revenus modestes Cela met en lumière un problème structurel dans le système de remboursement, où les inégalités d’accès aux technologies de traitement créent des disparités de soins. Les patients à faibles revenus sont souvent contraints de renoncer à des dispositifs pourtant essentiels pour une meilleure gestion de la maladie.
- Perte de productivité [20] :Le diabète a des répercussions significatives sur la productivité, tant au niveau individuel qu’économique. Les patients diabétiques peuvent faire face à des absences fréquentes pour des consultations médicales, des traitements ou en raison de complications liées à la maladie. Cette situation entraîne non seulement des coûts directs pour les entreprises, tels que le remplacement temporaire des employés absents, mais aussi des coûts indirects, comme la perte de savoir-faire et d’expérience. Cette analyse des coûts liés à la perte de productivité nous pousse à reconsidérer le problème initial en intégrant une dimension économique plus large.
3. Facteurs Socioculturels
Les facteurs socioculturels influencent à la fois la prévention et la gestion du diabète :
- Les habitudes de vie et l’alimentation [19]: Les changements socioculturels en France, tels que la consommation croissante de produits industrialisés et l’augmentation de la sédentarité, accentuent la progression du diabète de type 2. Cela confirme l’hypothèse initiale que les habitudes de vie et l’alimentation sont des facteurs déterminants dans la progression du diabète de type 2. Il apparaît que les efforts actuels pour sensibiliser les populations sur ces enjeux restent insuffisants, surtout auprès des personnes âgées ou moins éduquées.
- Perception du diabète [5] : Il existe encore une mauvaise compréhension de la maladie, en particulier concernant le diabète de type 2, souvent perçu comme une conséquence uniquement de l’alimentation, sans considération pour des facteurs génétiques ou autres déterminants de santé.
- Vieillissement de la population [1] : Le vieillissement de la population française est un facteur de risque supplémentaire pour l’augmentation des cas de diabète. Les seniors sont plus susceptibles de développer un diabète de type 2, nécessitant une prise en charge spécifique. Il est crucial de mener une étude sociologique approfondie sur la gestion du diabète chez les personnes âgées, en s’appuyant sur les travaux existants qui traitent de l’alimentation et de la santé des seniors. Les recherches de Philippe Cardon, par exemple, peuvent éclairer les défis quotidiens auxquels les personnes âgées sont confrontées dans la gestion de leur alimentation et leur santé. Cela renforcerait notre compréhension des lacunes dans le suivi des soins et des ressources nécessaires pour cette population vulnérable.
4. Facteurs Technologiques
L’analyse de ces technologies nous pousse à reconsidérer notre approche et à affiner notre problématique.
- Pompes à insuline et capteurs de glucose [1]: Les innovations telles que les pompes à insuline et les capteurs de glucose en continu améliorent considérablement la gestion quotidienne du diabète, notamment pour les patients atteints de diabète de type 1. Toutefois, l’adoption de ces technologies est entravée par des obstacles économiques, comme le coût élevé des dispositifs et la variabilité de leur remboursement par l’Assurance Maladie. Cette analyse montre que malgré les avancées technologiques, l’accès à ces dispositifs reste limité, notamment en raison de coûts élevés et d’une adoption inégale selon les régions. Ces barrières technologiques représentent un frein significatif dans l’amélioration des conditions de vie des patients.
- Téléconsultations et télésurveillance[11]: Le développement des services de santé numériques permet aux patients diabétiques d’accéder plus facilement à des soins et à des conseils médicaux via des plateformes de télémédecine. Ces outils sont particulièrement utiles pour les patients vivant dans des zones rurales ou éloignées des grands centres de santé. L’adoption de la télémédecine pourrait également conduire à une modification des activités des cibles. Nous pourrions explorer comment les structures de santé traditionnelles peuvent évoluer pour intégrer ces outils numériques, offrant ainsi un suivi plus personnalisé et régulier.
- Systèmes de boucle fermée [6] : Les systèmes de boucle fermée, qui permettent une gestion automatisée de l’insuline, représentent une avancée révolutionnaire dans la prise en charge du diabète. Ces technologies, encore en développement, promettent de réduire considérablement la charge de gestion quotidienne du diabète pour les patients, en permettant un contrôle glycémique plus précis et en minimisant les risques d’hypoglycémie. En nous concentrant sur l’innovation, nous pourrions affiner notre problématique : l’impact de l’automatisation sur la qualité de vie des patients et leur autonomie dans la gestion de leur condition.
5. Facteurs Environnementaux
L’environnement joue également un rôle dans l’incidence et la gestion du diabète :
- Urbanisation[1] : La forte urbanisation en France a des effets contrastés sur la santé. Si elle favorise l’accès aux soins, elle entraîne également une sédentarité accrue, aggravée par des infrastructures peu adaptées à l’activité physique (ex. : peu de pistes cyclables, modes de vie stressants).
- Pollution [9] : Des études suggèrent un lien potentiel entre l’exposition à certains polluants (comme les perturbateurs endocriniens) et un risque accru de diabète de type 2. Ces facteurs environnementaux commencent à être pris en compte dans les recherches sur les causes sous-jacentes de la maladie.
6. Facteurs Légaux
Le cadre législatif et réglementaire est crucial dans la gestion du diabète :
- Régulation des soins de santé [7] : La France bénéficie d’un système de Sécurité Sociale solide, avec une bonne couverture des traitements pour les patients diabétiques. Cependant, l’accès à certaines technologies innovantes, comme les capteurs de glycémie ou les pompes à insuline, peut être retardé par des questions réglementaires et de remboursement.
- Normes alimentaires [8]: Les réglementations concernant les étiquettes nutritionnelles et les taxes sur les boissons sucrées ont été renforcées dans le but de lutter contre l’obésité et les maladies liées, comme le diabète. Ces mesures visent à réduire la consommation de sucre, bien que leur impact réel soit encore débattu.
- Loi sur l’accessibilité [10]: Pour les personnes diabétiques, la question de l’accessibilité aux établissements publics ou aux écoles (ex. : gestion des téléphones portables pour les capteurs de glycémie) pose parfois des difficultés.
Présentation de notre problématique
Les informations recueillies lors de nos entretiens avec les différents acteurs du secteur, qu’il s’agisse de patients, de professionnels de santé ou de membres d’associations, nous ont permis de mieux cerner les défis liés à la prise en charge du diabète en France. Ces échanges ont révélé des enjeux cruciaux, comme la nécessité de meilleures informations pour les patients, l’amélioration de l’accès aux nouvelles technologies de traitement, et une prévention plus efficace face à l’augmentation constante des cas de diabète, notamment de type 2.
Fort de ces retours, nous avons affiné notre réflexion et sommes arrivés à la question centrale : Comment améliorer le suivi de la la glycémie des diabétiques non autonomes dans la prise en charge de leur maladie ? Ce cadre de travail nous a permis d’orienter le développement de notre solution et de l’adapter aux besoins des patients.
Notre solution
Les entretiens réalisés avec différents acteurs — patients, professionnels de santé et membres d’associations — ont été essentiels pour affiner notre cible. Ces échanges ont mis en lumière les besoins spécifiques des personnes âgées, un groupe particulièrement vulnérable dans la gestion quotidienne du diabète. Face à des problèmes d’autonomie, de mobilité et parfois des difficultés auditives ou cognitives, il est apparu que ces patients nécessitent une approche adaptée et simplifiée pour suivre leur glycémie de manière efficace.
Notre solution est spécialement conçue pour les personnes âgées, un groupe particulièrement vulnérable face au diabète, en particulier le diabète de type 2. Avec l’âge, la gestion quotidienne de cette maladie devient plus complexe, notamment en raison de la baisse de la mobilité, de la perte de mémoire, et parfois d’une moindre maîtrise des technologies modernes.
Nous voulons concevoir une solution facile d’utilisation, pensée pour être à la fois pratique et accessible. Le dispositif repose sur une technologie simple mais efficace. Il comprend un aimant avec un écran intégré, destiné à être placé sur le réfrigérateur, un endroit souvent visible dans le quotidien des personnes âgées. Cet écran affiche les courbes de glycémie en temps réel, et signale tout dépassement des seuils normaux en faisant passer la courbe en rouge, offrant ainsi un retour visuel immédiat. Cet écran peut également être utile aux infirmiers à domicile, leur permettant de consulter rapidement les constantes, et de rassurer les familles sur l’état de santé du patient.
Pour pallier les éventuels problèmes auditifs ou d’inattention, un bracelet vibrant est associé au dispositif. Celui-ci alerte le patient en cas de taux de glycémie anormal, même si la personne n’est pas à proximité de l’écran. L’ensemble de ce système fonctionne avec un capteur Freestyle fixé sur le bras du patient, qui transmet les données de glycémie en temps réel à l’écran via Bluetooth. Ce dispositif prend ainsi en compte les divers problèmes recensés lors des entretiens, offrant un suivi précis et sans nécessiter de manipulation complexe de la part des patients ou de leur entourage.
L’environnement réglementaire:
Dans le cadre du développement de notre solution de suivi de la glycémie, il est impératif de prendre en compte l’environnement réglementaire qui régit le secteur de la santé. La création d’un dispositif médical ne peut se faire sans respecter les exigences imposées par le Règlement (UE) 2017/745 sur les dispositifs médicaux (MDR), entré en vigueur le 26 mai 2021. Ce règlement impose des normes strictes pour assurer la sécurité et l’efficacité des dispositifs destinés à diagnostiquer, prévenir, surveiller ou traiter des maladies. En France, l’Agence nationale de sécurité du médicament et des produits de santé (ANSM) est l’autorité qui régule ces dispositifs, garantissant que notre solution respecte les normes de performance et de sécurité, comme celles définies par les normes ISO.
Par ailleurs, il est essentiel d’intégrer le respect du Règlement Général sur la Protection des Données (RGPD)[10] dans le développement de notre solution. Depuis mai 2018, le RGPD impose des obligations concernant la collecte et le traitement des données personnelles, un aspect fondamental pour garantir la confiance des utilisateurs. Pour notre dispositif, cela signifie que les données relatives à la glycémie doivent être traitées de manière sécurisée et transparente. Cela implique des pratiques telles que l’anonymisation des données, le consentement éclairé des patients pour le traitement de leurs informations, et l’établissement de protocoles robustes de sécurité pour prévenir tout accès non autorisé.
En intégrant ces considérations réglementaires dès le départ, nous nous assurons que notre solution non seulement répond à un besoin pressant de suivi de la glycémie, mais est également conforme aux exigences légales. Cela renforce sa légitimité et sa viabilité sur le marché, tout en protégeant les utilisateurs et en leur offrant une tranquillité d’esprit quant à la sécurité de leurs informations personnelles.
Références bibliographiques
[1] Fédération Française des Diabétiques. « Les chiffres du diabète en France » [Internet]. [cité le 6 octobre 2024]. Disponible sur: https://www.federationdesdiabetiques.org/information/diabete/chiffres-france
[2] Ministère de la Santé et de la Prévention. Diabète [Internet]. [cité le 6 octobre 2024]. Disponible sur: https://sante.gouv.fr/soins-et-maladies/maladies/article/diabete
[3] Haute Autorité de Santé. « Diabète de type 2: prévention, dépistage, prise en charge initiale » [Internet]. 2022 [cité le 6 octobre 2024]. Disponible sur: https://www.has-sante.fr/upload/docs/application/pdf/2022-11/ap_fiche_diabete_2.pdf
[4] American Diabetes Association. About Type 1 Diabetes [Internet]. [cité le 6 octobre 2024]. Disponible sur: https://diabetes.org/about-diabetes/type-1
[5] American Diabetes Association. About Type 2 Diabetes [Internet]. [cité le 6 octobre 2024]. Disponible sur: https://diabetes.org/about-diabetes/type-2
[6] Organisation Internationale de Normalisation. ISO 15197:2013. Systèmes d’autosurveillance du glucose sanguin – Exigences pour les systèmes destinés à des patients diabétiques [Internet]. [cité le 6 octobre 2024]. Disponible sur: https://www.iso.org/fr/standard/59752.html
[7] Organisation Internationale de Normalisation. ISO 20417:2021. Informations à fournir par le fabricant des dispositifs médicaux [Internet]. [cité le 6 octobre 2024]. Disponible sur: https://www.iso.org/fr/standard/72704.html
[8] Agence Fédérale des Médicaments et des Produits de Santé. Règlement relatif aux dispositifs médicaux et établissements de santé [Internet]. [cité le 6 octobre 2024]. Disponible sur: https://www.afmps.be/sites/default/files/content/POST/MEDDEV/07%20H%C3%B4pitaux%20et%20professionnels%20de%20la%20sant%C3%A9/MDR%20et%20%C3%A9tablissements%20de%20sant%C3%A9%20FR.pdf
[9] Faguer, R. Problématiques liées à la santé environnementale et risques. Environnement, Risques & Santé [Internet]. [cité le 6 octobre 2024]. Disponible sur: https://shs.cairn.info/revue-environnement-risques-et-sante-2018-1-page-8?lang=fr&contenu=resume
[10] Commission Nationale de l’Informatique et des Libertés (CNIL). Données de santé : La CNIL rappelle les mesures de sécurité et de confidentialité pour l’accès au dossier médical [Internet]. [cité le 6 octobre 2024]. Disponible sur: https://www.cnil.fr/fr/donnees-de-sante-la-cnil-rappelle-les-mesures-de-securite-et-de-confidentialite-pour-lacces-au
[11] Haute Autorité de Santé (HAS). Prévention du diabète de type 2 [Internet]. [cité le 6 octobre 2024]. Disponible sur: https://www.has-sante.fr/upload/docs/application/pdf/2022-11/ap_fiche_diabete_2.pdf
[12] Chen, S., Liu, X., Zhou, R., Huang, S., & Ding, X. Advances in the treatment of type 2 diabetes with novel therapeutics [Internet]. [cité le 6 octobre 2024]. Disponible sur: https://www.nature.com/articles/s41421-024-00662-3
[13] Fédération Française des Diabétiques. Dépression et diabète : quels sont les liens ? [Internet]. [cité le 6 octobre 2024]. Disponible sur: https://www.federationdesdiabetiques.org/information/risques/depression-diabete
[15] Diabète Magazine. La dépression et le diabète [Internet]. [cité le 6 octobre 2024]. Disponible sur: https://www.diabetemagazine.fr/la-depression-et-le-diabete/
[16] Scheen, A. J. Inhibiteurs de l’alpha-glucosidase pour le traitement du diabète de type 2 [Internet]. [cité le 6 octobre 2024]. Disponible sur: https://www.cochranelibrary.com/cdsr/doi/10.1002/14651858.CD005061.pub3/full/fr#:~:text=Les%20inhibiteurs%20de%20l’alpha%E2%80%90glucosidase%20(acarbose%2C%20miglitol,diab%C3%A8te%20sucr%C3%A9%20de%20type%202
[17] Agence Fédérale des Médicaments et des Produits de Santé. Règlement relatif aux dispositifs médicaux et établissements de santé [Internet]. [cité le 6 octobre 2024]. Disponible sur: https://www.afmps.be/sites/default/files/content/POST/MEDDEV/07%20H%C3%B4pitaux%20et%20professionnels%20de%20la%20sant%C3%A9/MDR%20et%20%C3%A9tablissements%20de%20sant%C3%A9%20FR.pdf
[18] Brahem A, Selmi I, Boughattas W, Kacem I, Hafsia M, Slim I, et al. L’absentéisme chez les patients diabétiques type 1 en activité professionnelle. Rev Med Brux [Internet]. 2019;40:71-7. Disponible sur: https://www.amub-ulb.be/system/files/rmb/old/fae665be9fe41752550ffa475b9fd13a.pdf
[19] Assurance Maladie. Diabète et alimentation: les fondamentaux [Internet]. [cité le 21 octobre 2024]. Disponible sur: https://www.ameli.fr/assure/sante/themes/diabete-adulte/diabete-vivre-quotidien/equilibre-alimentaire/diabete-alimentation-fondamentaux
[20]PRISE EN CHARGE DES PATIENTS DIABETIQUES AGES MANAGEMENT OF DIABETES IN ELDERLY [Internet]. [cité le 21 octobre 2024].Disponible sur:
https://www.omedit-normandie.fr/media-files/20340/publication-2017pdf.pdf
[21]Prise en charge des patients diabétiques de type 2 âgés en médecine générale : les leçons de l’étude S.AGES-Observatoire DiabèteManagement of aged type 2 diabetic patients by general practitioners: Lessons from the S.AGES-Observatoire Diabète study [Internet]. [cité le 21 octobre 2024].Disponible sur:Prise en charge des patients diabétiques de type 2 âgés en médecine générale : les leçons de l’étude S.AGES-Observatoire Diabète – ScienceDirect
[22] Etat de santé des personnes diabétiques en France : 1ers résultats de l’étude Entred 3 en métropole [internet]. [cité le 20 octobre 2024]. Disponible sur :
[23] Diabète de type 2 · Inserm, La science pour la santé [internet]. [cité le 20 octobre 2024]. Disponible sur : https://www.inserm.fr/dossier/diabete-type-2/#:~:text=L’incidence%20du%20DT2%20augmente,femmes%20trait%C3%A9s%20pour%20cette%20maladie.
[24] Feinkohl I, Sattar N, Welsh P, Reynolds RM, Deary IJ, Strachan MWJ, et al. (2012) Association of N-Terminal Pro-Brain Natriuretic Peptide with Cognitive Function and Depression in Elderly People with Type 2 Diabetes. [Internet]. [cité le 20 octobre 2024]. Disponible sur : PLoS ONE 7(9): e44569. https://doi.org/10.1371/journal.pone.0044569
[25] Medication adherence among the older adults : challenges and recommendations (2021). [Internet]. [cité le 20 octobre 2024]. Disponible sur :
https://www.hkmj.org/abstracts/v26n6/476.htm
[26] Upamali, S. et Rathnayake, S. (2023) ‘Perspectives of older people with uncontrolled type 2 diabetes mellitus towards medication adherence: A qualitative study’, [Internet]. [cité le 20 octobre 2024]. Disponible sur :
https://journals.plos.org/plosone/article?id=10.1371/journal.pone.0289834
WaterWatch – État de l’art – Eau et agriculture
État de l’art du projet: WaterWatch
Arrieta Emanuell, Carrijo Alex, Duval Evan, Levesques Jean-Philippe, Vidart Joaquin
Introduction de la problématique
Contexte Général
Environ 70 % de l’eau douce disponible dans le monde est utilisée par l’agriculture, mais seulement 65 % de cette eau est réellement absorbée par les cultures, ce qui entraîne une énorme inefficacité. Cette situation, combinée à la croissance rapide de la population mondiale, l’expansion de l’agriculture irriguée et les effets du changement climatique, exerce une pression énorme sur les ressources en eau douce. Depuis le début du 20ème siècle, la surface des terres irriguées a été multipliée par six, atteignant aujourd’hui plus de 260 millions d’hectares. Cependant, ces systèmes sont souvent inefficaces, avec des pertes d’eau significatives dues à des fuites et une gestion inadéquate.
Par exemple, bien que l’irrigation ne couvre que 20 % des terres cultivées, elle produit 40 % de la nourriture mondiale, ce qui montre son importance cruciale. Les régions comme l’Afrique du Nord, le Proche-Orient, l’Asie Centrale et l’Amérique Latine consacrent une part importante de leurs ressources en eau douce à l’agriculture.
Une grande partie de ces inefficacités est due aux fuites d’eau dans les vastes systèmes d’irrigation, difficiles à détecter et à réparer en raison des conditions hostiles des environnements de production. Ces fuites posent un sérieux problème pour la conservation des ressources en eau et la protection des écosystèmes locaux. [4, 6, 13]
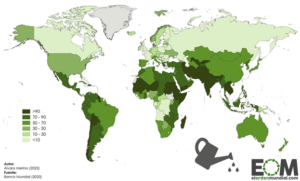
Pourcentage de l’extraction d’eau douce destinée à l’agriculture en 2020. Source : El Orden Mundial, 2023. [13]
Acteurs concernés
Analyse des rôles et intérêts des différents acteurs concernés :
- Éleveurs :
- Rôle : Acteurs principaux dans la production animale, notamment en Uruguay, où ils exploitent de vastes terrains pour l’élevage. Ils dépendent fortement de l’eau pour abreuver les animaux et irriguer les pâturages via des systèmes de canalisation étendus.
- Intérêts : Assurer un approvisionnement constant et fiable en eau pour maintenir la santé et la productivité de leurs troupeaux. Leur priorité est de garantir que les infrastructures de canalisation soient robustes et efficaces pour éviter les pertes d’eau et réduire les coûts de gestion.
- Céréaliers :
- Rôle : Producteurs agricoles opérant dans des régions où les conditions climatiques rendent l’irrigation indispensable pour maintenir des rendements suffisants. Ils dépendent d’un pompage régulier de grands volumes d’eau pour garantir la viabilité de leurs cultures.
- Intérêts : Maximiser la production tout en minimisant les coûts liés à l’eau. Ils recherchent des solutions technologiques pour optimiser l’irrigation, mais sont confrontés à la difficulté de gérer durablement les ressources hydriques dans des environnements aux conditions peu favorables.
- Maraîchers :
- Rôle : Producteurs de légumes dont les systèmes de production sont particulièrement intensifs et exigeants en eau. Ils doivent maintenir un contrôle strict des systèmes d’irrigation pour garantir des conditions optimales de croissance.
- Intérêts : Garantir une gestion rigoureuse et précise de l’eau pour éviter toute défaillance qui pourrait compromettre la qualité et le rendement des cultures. L’optimisation de l’irrigation est cruciale pour assurer la rentabilité et la pérennité de leur activité.
- Gouvernements et Organisations Non Gouvernementales (ONG) :
- Rôle : Régulateurs et défenseurs des ressources naturelles, impliqués dans la gestion des politiques de l’eau et la régulation de son utilisation dans le secteur agricole.
- Intérêts : Promouvoir des pratiques agricoles durables tout en préservant les ressources hydriques pour les besoins futurs. Ils s’efforcent de trouver un équilibre entre l’utilisation de l’eau pour l’agriculture et la préservation des écosystèmes naturels, tout en répondant aux besoins des communautés locales.
- Communautés locales :
- Rôle : Acteurs directement affectés par la gestion de l’eau, à la fois comme consommateurs d’eau potable et comme participants dans le débat sur l’usage des ressources naturelles.
- Intérêts : Assurer un accès durable à l’eau potable et la protection des aquifères, qui sont menacés par la surexploitation agricole. Elles s’inquiètent des impacts à long terme de la consommation d’eau excessive sur les réservoirs naturels et les écosystèmes environnants.
On remarque donc que chaque partie prenante a un intérêt fort dans la gestion efficace et durable de l’eau, qu’il s’agisse d’optimiser les rendements agricoles ou de préserver les ressources naturelles pour les générations futures. Les éleveurs, céréaliers et maraîchers cherchent à maximiser l’efficacité de leur usage de l’eau, tandis que les gouvernements, ONG et communautés locales travaillent à réguler cet usage pour éviter une surexploitation nuisible.
Enfin nous allons analyser les impacts que pourrait avoir notre solutions sur les différents acteurs. Une meilleure gestion de l’eau aurait des effets positifs importants pour chaque partie prenante. Les éleveurs et les producteurs de céréales et de légumes verraient une augmentation raisonnable de la production agricole, qui est plus durable et nécessite un minimum de coûts d’exploitation concernant l’irrigation. Leurs activités agricoles pourraient être plus stables même si leur situation géographique les confrontaient à des saisons difficiles sans précipitations. Ils pourraient également prendre des risques moins importants par rapport aux récoltes perdues si de mauvais systèmes d’irrigation faisaient défaut en raison de l’eau rare. Pour les gouvernements et les ONG, des politiques mises en place permettraient de préserver les systèmes aquifères, avec de l’eau propre accessible pour les générations à venir et une faible pression sur les écosystèmes aquatiques. En outre, les communautés locales bénéficient également des impacts positifs de telles améliorations car elles amélioreraient la sécurité de l’approvisionnement en eau, réduisant ainsi les conflits associés à la répartition de l’eau ainsi qu’à la qualité de vie. Enfin, la gestion durable et équilibrée de l’eau contribuerait à atténuer ses impacts négatifs sur l’environnement, garantissant la durabilité des pratiques agricoles et la protection des écosystèmes naturels.
Éco-Système visé
Pour définir l’écosystème de notre projet, nous réalisons une analyse PESTEL (politique, environnementale, sociale, technologique, économique et juridique) en tenant compte du contexte décrit ci-dessus. Sur le plan politique, nous examinons les réglementations existantes concernant l’utilisation des ressources en eau et les organisations impliquées. Au niveau social, nous analysons les implications de l’utilisation intensive de cette ressource et son impact sur la société en cas d’abus. En ce qui concerne la technologie, nous étudions les technologies actuelles et la manière de développer un projet organique en utilisant les systèmes existants. Nous évaluons également les coûts économiques liés à l’utilisation des systèmes d’eau et les opportunités potentielles de réinvestissement. Enfin, nous prenons en compte les aspects juridiques susceptibles d’influencer le développement de notre solution.
Politique :
L’agriculture, en particulier l’irrigation, est fortement encadrée par la législation. Pour toute exploitation agricole, le prélèvement d’eau pour l’irrigation nécessite une autorisation préalable auprès de la Direction Départementale des Territoires et de la Mer (DDTM). De plus, la création de forages ou de pompages en rivière est soumise à déclaration, et les volumes d’eau prélevés doivent respecter les quotas fixés.
L’irrigation peut être restreinte en cas de sécheresse par des arrêtés préfectoraux, encadrés par l’arrêté-cadre sécheresse, ce qui peut limiter les usages de l’eau par les agriculteurs. Ces restrictions peuvent encourager les exploitants à rechercher des solutions pour mieux gérer et surveiller leur consommation d’eau, comme les technologies de détection de fuites.
Enfin, certains départements, comme le Rhône, offrent des subventions pour aider les agriculteurs à investir dans des technologies liées à la gestion de l’eau. Ces subventions couvrent environ 30 % des coûts éligibles, avec un bonus de 10 % pour les jeunes agriculteurs ayant bénéficié de la Dotation Jeune Agriculteur (DJA). [1]
En Uruguay, la législation sur l’irrigation encourage les agriculteurs à améliorer leur capacité d’irrigation tout en promouvant la durabilité. La récente loi sur l’irrigation facilite les investissements, mais les procédures administratives pour obtenir des autorisations sont longues, et les coûts d’installation restent élevés. Les autorités locales offrent des incitations fiscales, mais l’efficacité de la régulation reste une préoccupation. [16]
Économique :
Les aides directes versées aux agriculteurs dans le cadre de la Politique Agricole Commune (PAC) jouent un rôle crucial dans la viabilité des exploitations agricoles. Entre 2020 et 2022, elles représentaient en moyenne 64 % du revenu courant avant impôt pour les exploitations agricoles en France. Ces aides sont cruciales pour la viabilité financière des agriculteurs, notamment dans certains secteurs comme l’élevage de bovins viande, où elles peuvent atteindre jusqu’à 210 % du revenu courant avant impôt (RCAI). En revanche, d’autres secteurs, tels que le maraîchage, sont moins soutenus (22 % du RCAI) .
Cette dépendance aux aides rend les agriculteurs vulnérables aux changements dans la politique de subvention et aux conditions économiques, ce qui peut influencer leur capacité à investir dans des solutions technologiques comme la détection de fuites d’eau. Environ 15 % des exploitations françaises sont particulièrement fragiles économiquement, cumulant une faible productivité et une forte dette. Cela pourrait limiter leur accès aux technologies coûteuses sans un soutien financier supplémentaire ou des subventions spécifiques.
D’un autre côté, la rentabilité de certaines exploitations, plus performantes économiquement, peut permettre des investissements plus aisés dans des systèmes de gestion de l’eau, surtout si ces technologies permettent de réaliser des économies d’eau et d’énergie à long terme. [15]
L’Uruguay est en train d’améliorer ses infrastructures agricoles avec des subventions pour moderniser les systèmes d’irrigation. Cependant, le coût des infrastructures d’irrigation reste un frein économique pour beaucoup de petits exploitants. Le gouvernement accorde des exonérations fiscales pouvant couvrir jusqu’à 100 % des investissements dans les systèmes d’irrigation, mais cela reste insuffisant pour certains. [7]
Social :
Les agriculteurs entretiennent une relation étroite avec l’eau, élément indispensable à leurs activités, et gèrent cette ressource depuis des siècles. Face aux enjeux climatiques actuels et aux réglementations imposées par les institutions étatiques, les agriculteurs doivent adopter des pratiques plus durables, en particulier en ce qui concerne l’utilisation de l’eau.
Il existe une forte pression pour réduire la consommation d’eau et améliorer la gestion des ressources naturelles. Les agriculteurs sont donc généralement ouverts à l’adoption de nouvelles solutions qui leur permettent de gérer plus efficacement leurs ressources. L’objectif est non seulement de minimiser les pertes d’eau, mais aussi de réduire les coûts liés aux factures d’eau et d’énergie, tout en renforçant leur engagement en faveur d’une agriculture plus écoresponsable. [11]
En Uruguay, l’agriculture est un pilier culturel, notamment dans les régions rurales. Aujourd’hui la perception de la gestion de l’eau commence à évoluer en raison de sécheresses récurrentes et de l’impact qu’elles ont sur les ressources en eau. Les agriculteurs uruguayens sont également de plus en plus ouverts aux solutions innovantes, mais leur adoption dépend largement des incitations économiques et de la disponibilité des technologies. [16]
Technologique :
En France, les agriculteurs ont accès à diverses technologies pour améliorer la gestion de l’eau, telles que des capteurs de pression, des systèmes de pompage automatisés, et des outils numériques pour suivre la consommation d’eau. Le développement de technologies telles que l’Internet des objets (IoT) et les systèmes de gestion intelligents de l’eau a permis une gestion plus fine des ressources hydriques, bien que l’adoption de ces technologies soit encore limitée dans certaines régions rurales.
Aujourd’hui, pour faire face à ce problème, certaines entreprises proposent des services de remplacement du système de canalisations existants afin d’en installer un nouveau connecté pour avoir des informations sur tout le réseau d’eau à l’instant t. L’inconvénient de ce système est qu’il nécessite le remplacement de tout le réseau d’eau ce qui peut impliquer un coût très important.
D’autres alternatives existent, comme par exemple la détection de fuites par l’acoustique. En effet, la présence d’une fuite provoque un bruit significatif à son emplacement, par conséquent, il existe une méthode à partir d’appareils sensibles au son pour détecter le bruit de l’eau s’écoulant à travers une fissure ou une canalisation endommagée. Cette méthode est peu coûteuse mais nécessite énormément de temps afin de passer au peigne fin tout le réseau d’eau. Elle n’est pas envisageable sur un réseau de plusieurs kilomètres.
L’Uruguay cherche également à adopter des technologies modernes pour la gestion de l’eau, mais l’accès est inégal entre les grandes exploitations et les petits agriculteurs. Les technologies low-tech et les solutions autonomes, comme les systèmes de détection de fuites, pourraient aider à améliorer l’efficacité de la gestion de l’eau dans les zones rurales mal desservies. Cependant, les contraintes économiques freinent parfois leur adoption.
Environnemental :
La gestion durable des ressources en eau est au cœur des préoccupations agricoles actuelles, en particulier dans un contexte de changement climatique et de sécheresses fréquentes. Les pressions environnementales ont conduit à des régulations plus strictes sur les prélèvements d’eau, avec un accent sur la conservation des ressources. Les solutions visant à limiter les pertes d’eau sont donc cruciales pour s’adapter à ces nouvelles conditions. [6]
De même l’Uruguay est fortement affecté par le changement climatique, avec des sécheresses de plus en plus fréquentes qui perturbent les systèmes d’irrigation. La conservation de l’eau est devenue une priorité nationale, avec des efforts pour promouvoir des pratiques agricoles plus durables.
Légal :
En France, la législation sur la gestion de l’eau pour l’agriculture est stricte. Les prélèvements d’eau doivent être autorisés, et les exploitations agricoles doivent se conformer à des règles spécifiques selon les volumes d’eau utilisés. En période de sécheresse, des arrêtés préfectoraux limitent les prélèvements pour protéger les ressources naturelles. La conformité à ces lois est essentielle pour éviter des amendes et des restrictions supplémentaires. Pour ce qui est de l’Uruguay, bien que l’irrigation soit encouragée, les agriculteurs doivent également obtenir des autorisations pour l’utilisation de grandes quantités d’eau. Cependant, les délais administratifs sont un obstacle majeur, et de nombreuses petites exploitations rencontrent des difficultés à se conformer à toutes les exigences légales.[10]
Littérature Scientifique
Pertes d’eau et coûts
La gestion de l’eau est une préoccupation majeure dans l’agriculture, notamment en raison des coûts élevés associés aux infrastructures de distribution d’eau et aux pertes. Aux États-Unis, par exemple, environ 7 000 km de tuyaux doivent être remplacés chaque année, ce qui coûte environ 2,7 milliards de dollars, tandis que les pertes d’eau, estimées à 10 %, entraînent une perte de près de 4,3 milliards de dollars par an [17] . Dans d’autres pays comme l’Angleterre, la France et l’Italie, les pertes d’eau oscillent entre 20 et 30 % [4] . Ces chiffres soulignent la nécessité d’améliorer les pratiques de gestion de l’eau, notamment dans le secteur agricole, où l’augmentation des besoins d’irrigation exerce une pression supplémentaire sur les ressources en eau.
L’efficacité de l’irrigation, qui est un enjeu clé en agriculture, reste relativement faible. Les surfaces irriguées augmentent d’environ 1 % par an, et la demande en eau pour l’irrigation devrait croître de 13,6 % d’ici 2025 [4] . Cependant, entre 8 et 15 % des réserves d’eau douce devraient être détournées de l’agriculture pour répondre aux besoins croissants des usages domestiques et industriels. Actuellement, seulement 55 % de l’eau utilisée pour l’irrigation est effectivement absorbée par les cultures, ce qui souligne l’importance de l’adoption de technologies améliorant l’efficacité de l’utilisation de l’eau.
Équipements et solutions de surveillance technologique
Il existe un manque général de capacités de surveillance avancée et d’analyse en temps réel dans de nombreux systèmes de distribution d’eau. Cependant, des événements clés comme les ruptures de tuyaux ou les ouvertures et fermetures de vannes peuvent être détectés à distance grâce à l’observation des transitoires de pression, qui diffèrent des signaux de pression de fond [17] . Les technologies de détection sans fil ont considérablement progressé, rendant possible le déploiement de réseaux denses de dispositifs à faible coût pour la surveillance en temps réel des infrastructures.
L’adoption de technologies comme le microcontrôleur ESP32 a également ouvert la voie à des systèmes de surveillance plus sophistiqués dans l’agriculture. L’ESP32 offre une connectivité Wi-Fi et Bluetooth, une puissance de calcul et une compatibilité avec divers protocoles de communication [2] . Son fonctionnement en basse consommation et ses blocs de sécurité matérielle en font un choix idéal pour les systèmes de surveillance en temps réel dans les applications de gestion de l’eau.
Produits et solutions existants
Plusieurs solutions visant à automatiser et optimiser la gestion de l’eau dans l’agriculture existent déjà. Par exemple, Lorentz propose des pompes télécommandées, offrant une plus grande flexibilité et un meilleur contrôle du fonctionnement des pompes [12] . Cependant, ces systèmes sont généralement vendus en tant que package avec la pompe, limitant ainsi leur intégration dans les réseaux de systèmes existants.
D’autres solutions innovantes incluent le système « Buena Huella », qui intègre divers capteurs pour une meilleure gestion des bâtiments, tels que des capteurs de niveau d’eau et de température [3] . Des entreprises comme Kivoy fournissent également des pompes à eau connectées, améliorant ainsi la gestion des ressources et l’efficacité des équipements [9] . IrriControl propose des fonctionnalités supplémentaires telles que la surveillance en temps réel de la consommation d’eau et des alertes de panne, contribuant ainsi à une utilisation plus efficace des ressources et à une meilleure fiabilité opérationnelle [8] .
Ces systèmes existants soulignent l’importance de développer des innovations visant à simplifier les dispositifs, à augmenter leur fiabilité et à réduire leur coût. L’utilisation de telles technologies peut conduire à une meilleure gestion de l’eau en agriculture, réduisant à la fois le gaspillage et les coûts d’exploitation [5] .
L’automatisation des pompes agricoles est essentielle pour répondre aux défis posés par l’augmentation de la demande en eau, les inefficacités de l’irrigation et les coûts élevés des pertes d’eau. Le développement et le déploiement de systèmes de surveillance avancés et l’intégration de technologies de contrôle en temps réel, telles que l’ESP32, ont le potentiel d’améliorer considérablement la gestion de l’eau en agriculture. En adoptant ces innovations, le secteur agricole peut mieux gérer les ressources en eau, améliorer le rendement des cultures et réduire les coûts d’exploitation.
Solution proposée
Pour détailler notre proposition de solution, nous commençons par le diagramme suivant, qui illustre ce que nous voulons réaliser. Ensuite, nous expliquerons le système et chacun des éléments nécessaires à son fonctionnement.
Les premiers éléments d’intérêt sont les capteurs, qui seront répartis dans tout le système de canalisation d’eau. C’est ici que surgit l’un de nos premiers défis : trouver une distribution optimale pour eux. Les capteurs sont une partie fondamentale du système de contrôle, car ils sont responsables de surveiller constamment la pression de l’eau dans les tuyaux. Comme mentionné dans [17], lorsqu’une fuite d’eau se produit, il y a une perte de pression dans tout le système, et par la suite, la pression commence à fluctuer de manière à ne jamais se stabiliser complètement. Ce comportement peut être observé dans les figures suivantes :
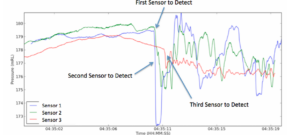
Traces de pressions montrant un transitoire initial.You Traduce al frances: Fuente : Whittle et al, 2013. Source : Whittle et al, 2013. [17]
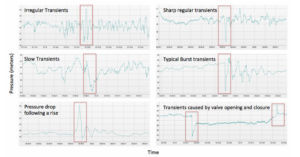
Traces de pressions montrant un transitoire initial.You Traduce al frances: Fuente : Whittle et al, 2013. Source : Whittle et al, 2013. [17]
Grâce à ces modules, toutes les informations recueillies par les capteurs seront envoyées de manière efficace et fiable au microcontrôleur, qui est le dernier élément de notre système et le plus important. Le microcontrôleur traitera les données reçues, effectuera les opérations nécessaires et notifiera l’utilisateur final des événements détectés. De plus, le système offrira la possibilité de fermer à distance le flux d’eau pour éviter les pertes en cas de détection de pannes ou de fuites, améliorant ainsi l’efficacité et le contrôle du système de stockage d’eau. Cela se fera via une application web ou mobile qui fournira un environnement convivial pour l’utilisateur final.
Enfin, bien que le système proposé soit axé sur la résolution de certains besoins du secteur agricole, cela n’implique pas que le système ne puisse être mis en œuvre dans d’autres domaines, car il est censé être suffisamment flexible et adaptable à diverses situations. Mais surtout, le système doit être utile, accessible et durable dans le temps.
Références bibliographiques
[1] Aider à la gestion de l’eau. (n.d.). Disponible sur:
https://aides-territoires.beta.gouv.fr/aides/4732-aider-a-la-gestion-de-leau/
[2] Bertoleti, P. (2019). Projetos com ESP 32 e LoRa. Disponible sur:
https://www.google.fr/books/edition/Projetos_com_ESP32_e_LoRa/fnCiDwAAQBAJ?hl=pt-BR&gbpv=1
[3] Buena Huella. (2023). Disponible sur:
https://buenahuella.com.ar/productos.php#monitoreo
[4] Chartzoulakis, K., & Bertaki, M. (2015). Gestion durable de l’eau en agriculture face au changement climatique. Agriculture and Agricultural Science Procedia. Disponible sur:
https://www.sciencedirect.com/science/article/pii/S2210784315000741
[5] De Varennes, E. M., & Mendonça, P. (1970). Automaticité des stations de pompage des réseaux d’irrigation, d’assainissement agricole et de distribution rurale d’eau potable.
[6] Enjeux environnementaux : L’eau, les sols. (2021, 28 mai). Disponible sur:
https://agriculture.gouv.fr/enjeux-environnementaux-leau-les-sols
[7] Farmaland Uruguay. (n.d.). Fiscal incentives for farms in Uruguay. Disponible sur:
https://farmlanduruguay.com/investments/investment-promotion-for-farms-in-uruguay/
[8] IrriControl. (2024). Disponible sur:
https://irricontrol.com.br/servicos/
[9] Kivoy. (2024). Disponible sur:
https://kivoy.com.uy/catalogo/
[10] Le règlement général sur la protection des données (RGPD). (2023, 11 avril). Disponible sur:
https://www.economie.gouv.fr/entreprises/reglement-general-protection-donnees-rgpd
[11] L’eau et l’agriculture. (n.d.). Disponible sur:
https://www.artois-picardie.eaufrance.fr/qui-contacter-a-propos-de/l-eau-et-l-agriculture/
[12] Lorentz. (2024). Produits connectés. Disponible sur:
https://www.lorentz.de/es/productos-y-tecnologia/productos/connected/
[13] Merino, A. (2023). ¿Cuánta agua se destina a la agricultura en el mundo? El Orden Mundial EOM. Disponible sur:
https://elordenmundial.com/mapas-y-graficos/cuanta-agua-se-destina-a-agricultura-mundo/?form=MG0AV3
[14] Pourquoi l’eau est-elle au cœur des enjeux? Quels scénarios possibles dans un contexte de dérèglement climatique? (n.d.). Disponible sur:
[15] Résultat économique des exploitations agricoles et revenu des agriculteurs, une très grande hétérogénéité. (2024, 27 février). Disponible sur:
[16] Scasso, F. (2019, 7 juin). Protéger les terres et la biodiversité en Uruguay. United Nations Development Programme. Disponible sur:
https://www.undp.org/blog/protecting-land-and-biodiversity-uruguay
[17] Whittle, A. J., et al. (2013). Sensor networks for monitoring and control of water distribution systems. In Proceedings of the International Conference on Structural Health Monitoring of Intelligent Infrastructure (Vol. 6). Hong Kong. Disponible sur:
Cartographie 3D
Cartographie 3D
Pour obtenir une carte avec une imprimante 3D
Ce site vous permet de sélectionner la zone géographique qui vous intéresse et d’exporter le fichier en .stl. Il ne vous reste plus qu’à le transformer en gcode pour l’imprimante 3D !
Petit conseil : redimensionner votre carte en jouant sur l’axe des z dans votre logiciel de slicing pour avoir un bon rendu.
Pour obtenir une carte avec des aplats superposés
Ce site vous permet de sélectionner la zone géographique qui vous intéresse et d’exporter le fichier en .stl. Le logiciel Slicer for Fusion 360 vous permet de découper ce modèle 3D en couches. Pour plus de détails sur les différents types de découpe (appelées « Construction technique ») possible, ce tuto est très bien.
Ici on choisira « stacked slices ». L’onglet « get plans » permet de visualiser les plans. Un bouton en bas de page permet d’exporter sur l’ordinateur en différents formats (par exemple pdf).
Ouvrir ce pdf sur inkscape ou Corel Draw afin de bien paramétrer pour la découpe. Découper. Coller dans le bon ordre les différents aplats !
Pour obtenir une carte customisée
Sélectionner votre zone sur Open Street map par exemple.
La plaque de bois du fond peut être peinte (en bleu s’il y a de l’eau) ou gravée avec des détails du fond.
Créer un fichier pour les rues : pour cela importer votre carte open street map (même une impression écran suffira), vectorisez-la ou faite le tracé des rues à la main avec l’outil courbes de Bézier. Attention à l’épaisseur des ruelles et ajouter bien un cadre de 1 cm tout autour ! Découper à la découpeuse laser. Coller la découpe des rues sur le fond de carte en bois.
Pour obtenir une carte topographique à partir d’un bloc de bois
Mekanika a fait un super tuto ! Il s’agit de fraisage à la fraiseuse CNC.
Communication peer to peer LoRa-E5 | Arduino Leonardo
Prérequis
Arduino Leonardo[1] |
Module Grove Base Shield[2] |
Module LoRa-E5 Grove[3] |
Connecteur UART[4] |
![]() |
![]() |
![]() |
Afin de mettre en place cette communication, j’ai dû m’inspirer du code de Sylvain Montagny présent sur son github[5].
Pour simplifier les choses, j’ai séparé la partie réception de la partie transmission mais chaque carte est en mesure d’envoyer et recevoir des informations.
Les prochaines illustrations et tests ont été effectués à l’aide du logiciel « Arduino IDE » téléchargeable sur cette page[6].
Amélioration de Primo de Cubetto
Dans le cadre du projet CODEVSI, un groupe de 3 étudiants s’est vu confier la tâche de d’améliorer les fonctionnalités de la version open source du robot Cubetto.
Le Cubetto est un robot destiné à l’enseignement des bases de la programmation aux enfants, permettant une introduction ludique et interactive au codage.
Il est composé d’un robot motorisé en bois, d’un tapis sur lequel il se déplace et d’une interface de commande permettant de programmer ses mouvements à l’aide de blocs physiques.
Un problème majeur a été identifié dans la version open source : le manque de précision dans les déplacements du robot dû au système de pilotage des roues. Ce dernier utilisait un capteur optique couplé à un moteur à engrenages, pour suivre la rotation des roues en comptant les
traits noirs et blancs.
Le groupe a conçu une solution de remplacement, incluant une modification complète du système de pilotage :
– des moteurs pas à pas 28BYJ-48 disponibles au Fablab ont remplacé les moteurs à engrenage
– les drivers moteurs associés ont été remplacés
– le code Arduino a été modifié en conséquence pour asservir le moteur pas à pas
– une breadboard a été ajoutée pour assurer l’alimentation des deux moteurs
Pour assurer la meilleure précision possible, il a été nécessaire de :
– modéliser puis imprimer en 3D un joint d’adaptation entre la roue et l’arbre-moteur
– modéliser puis réaliser en 3D un support de fixation pour le moteur sur la carrosserie
Par ailleurs, une nouvelle fonctionnalité de détection des obstacles a été ajoutée. Ceci est réalisé à l’aide d’un capteur ultrason de modèle HC-SR04 lui aussi disponible au Fablab.
Le code Arduino principal a intégré le fonctionnement du capteur optique.
Finalement, une nouvelle carrosserie a été fabriquée à l’aide de la découpeuse laser du Fablab pour être adaptée au nouveau capteur ultrason et pour contenir l’ensemble des nouveaux composants.
Une fois le nouveau modèle assemblé, une série de tests a été exécutée pour vérifier le bon fonctionnement du robot et du nouveau système, assurant ainsi que les améliorations apportées répondaient aux attentes et aux exigences du projet.
Membres du groupe : Khalil SOUGUIR, Ylan TEISSIER, Marie-Joséphine EDOA
Annexes :
Code Arduino du robot
Joint d’adaptation entre la roue et l’arbre-moteur
Objets animés
Phare animé, tableau marin lumineux, oiseaux animés… De nombreux objets peuvent être conçus avec les élèves et animés grâce à de la programmation graphique, des LEDs et des servomoteurs !
Voici un exemple de phare lumineux réalisé pour des animations en classe de CM2 à Bourg Blanc (article ici) et en CM1/CM2 à Coray avec la mallette MERITE « Objets animés ».
Le fichier utilisé pour le phare de démonstration est disponible ici. Il a été découpé sur une plaque de CP peuplier 3mm.
La partie du haut n’est pas collé à celle du bas (pour le transport et pour montrer l’assemblage aux élèves). Une face latérale du phare reste également amovible. La LED et le servomoteur tiennent avec de la patafix. Un autre trou permet aussi de mettre le servomoteur dans la partie du haut. Les autres faces de la parties du bas sont collées à la colle à bois, de même que les faces de la partie du haut.
En se servant de la mallette on peut aussi aller plus loin avec des boutons poussoirs, des photorésistances… Tout dépend du projet !
Le projet avec les phares a été fait en 3h30 + 2h pour la partie programmation, plus 2h pour la partie réalisation du phare des élèves.